The End Game
A project has to have an "end game" to steal the concept from Chess. There comes a time not to "chase the rabbit down the hole".
While laser cutters are very precise, they still have the same accuracy issues common to CNC mills.
Accuracy versus Precision
When I was young a had a wind up wrist watch. My watch had a second hand, but it usually off by about 5 minutes a day. So it has a precision of 1 second but an accuracy of 5 minutes. Think about this as it is important!
CNC machines are very precise, usually better than 1/100 of a mm, but how accurate are they? That depends on many things and how hard you drive them.
When I first started using my CNC mill, I drove it hard and fast. The result was that my circle cut outs were visibly oval in shape and not to size (at least a 1 mm too small).
When using CNC machines, it is necessary to slow down and reduce the depth of the cut (to unload the machine) and to compensate for the cut (i.e. conventional or climb cut etc) if you want accuracy.
What I have noticed in the videos of the laser cut gears is that they suffer the same problems (but not so bad) as my gear box. Their gears are also noisy and wobble around.
What this tells me is that laser cutters do not have the accuracy necessary to cut very fine gear teeth. Laser Cutting Services are going to run their machines fast as most clients don't have the need for high accuracy, especially in "Z".
You can see from the image of the sun gear that the teeth are cut very precisely:
That is at least to 1/10 of a millimetre. But the not very accurately, tilted.
Another Laser Cutter Service Provider
I seek out another laser cutter service provider. The one uses a bigger machine and is more expensive (~50%). But her can cut 6 mm plywood and acrylic. Nice.
The kerf for his machine is about 0.3 mm versus about 0.15 mm for the previous service.
Backlash Still Too High
The backlash for my gear box is less than one degree (which is not too bad) but far too high for my intended application (a SCARA elbow). Although I can improve the accuracy of the gears by making the teeth bigger (i.e. change the diameter and gearing ratio of the gear box), and using another (hopefully more accurate laser cutter service provider), the backlash for the gear box will likely still be too high.
There are still options that can be pursued. One thought is a lantern design:
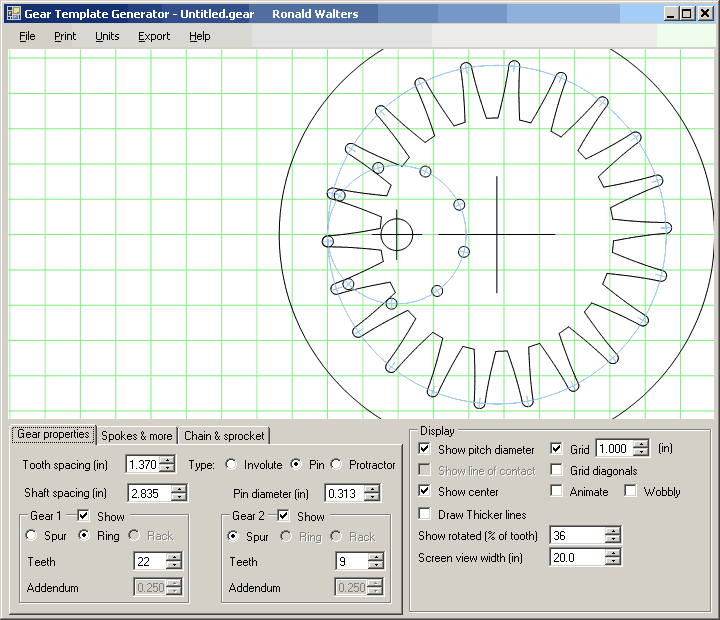
Here the accuracy is determined by the location of the socket and pin holes. The machine would very lightly loaded drilling (rather than cutting) these, so likely to be more accurate (than cutting). The pins themselves are very accurate.
One advantage of the lantern design is I can cut it with my CNC machine.
But, for my application I think I may be better off exploring a belt drive and custom belt gears. Time is an issue as well.
AlanX
Discussions
Become a Hackaday.io Member
Create an account to leave a comment. Already have an account? Log In.
Yeah, if you need zero backlash then belts are better. You can even still use the same underlying principle as this mechanism. Check out Skyentific's channel if you haven't seen it https://www.youtube.com/watch?v=Z0rGd7UO2Tk
But his demo unit there has pretty low torque capacity due to lack of belt tension adjustment and the weak attachment to the motor rotor as the planet carrier. The strongest carrier design I've come up with is simply a square tube, driven via the motor shaft (motor outside the mechanism, square tube between the pulleys). But it still lacks tension adjustment, and I can't think of a good way to add that without also adding a lot of spinning mass.
Are you sure? yes | no
I made a quick 3D model of the square tube carrier https://i.imgur.com/GdwMmFQ.png
The three forces the carrier has to deal with are bending as it transmits the motor input torque out to the small pulley shafts, compresson as the small pulleys pull toward the center under load, and torsion as the small pulleys try to tilt sideways when they transfer power between the two large pulleys (here's an image showing how the tight and slack sides of the belts alternate under load to cause the torsion on the carrier https://i.imgur.com/P481TKi.png )
So the question is how do we make it possible to adjust tension on the belts, while still transmitting those forces effectively?
Are you sure? yes | no
Oh wow! You guys are trying to do this without an laser cutter of your own! This defeats the main benefit of laser cutting: producing a new set of parts in a few minutes if not seconds.
But yes, I guess this is not going to work for the precision needed for an robot arm. For this is might be easier to go for a belt drive. May be a laser cut version of https://hackaday.io/project/21355-reprap-helios is an option.
Are you sure? yes | no
That is a big machine!
Belt drive was the original upgrade path from my Prototype SCARA . The problem was the bearing design. MPRT basically does not need a bearing.
Anyway I am looking a a slew bearing at the moment. The other option is to look at two roller bearings.
AlanX
Are you sure? yes | no
Two roller bearings - which can be much smaller - sounds like the easier and cheaper option. Especially as the slew bearing will also need a second bearing to pre-load it.
Are you sure? yes | no
I am not going anywhere, but I know when it is time to move on. The problems with accuracy of CNC machines is well know to me. I am just surprised that commercial laser cutters are nearly as bad. I have learned this lesson from previous failed projects.
Just look at this video at the 1:45, he has the same "wobble".
---
On another topic, have a look at this:
https://www.youtube.com/watch?v=9DhPwtCZ9u4
He makes it look so easy.
AlanX
Are you sure? yes | no
I just thought of how to get rid of your slew bearing requirement. Use a double shaft stepper and put a transmission on both the top and bottom. It drops this down to a thickness where you can use a single bearing in the top layer then and avoids the need for such a tall Sun.
Are you sure? yes | no
You know AlanX, I would be willing to print some stuff out for you and ship it. If it fits in a regular envelope (max thickness of about 6mm), I believe the cost even going from the USA to Australia, is about $5. It may take a month to get there, but still. I do have a much better than average 3D printer, if you haven't seen it. :)
I do like your distinction of accuracy versus precision. Not many people stop to think about that.
Are you sure? yes | no