Time for another experiment for magnetic coupling between the internal and external of the enclosure.
This experiment differs from the first in two ways:
- By using magnets attached to a piece of paper, glued onto the servo horn. This is to mimic the flexibility of a sturdier material that could be used, such as Delrin or thin HDPE, or TPU / TPE flexible 3D printing filament. The idea is that the force of the magnets would bend the material to make the closest contact possible.
- By using magnets around the circumference in that plane via ‘petals’. Since the material is flexible, the petals can bend on installation, allowing it to fit through the narrow enclosure opening.
The hypothesis of this experiment is that the holding force will increase given the better contact between the internal and external magnets because of the flexible material.
Here is how the experiment was constructed. Magnets were enclosed into 3D printed ‘chicklets’. This was so that the hot glue would be attached to the enclosure and not stick to the magnets - as to ruin the dimensionality. These magnets then are glued onto a piece of cardstock paper. With some bending, it was able to fit into the enclosure. The magnets used in this experiment are the thin ones, at 3.175 mm tall. (We have alternate ones, at 7.65 mm tall.)
The results of the experiment disproved the hypothesis.
Here’s a look at it in action:
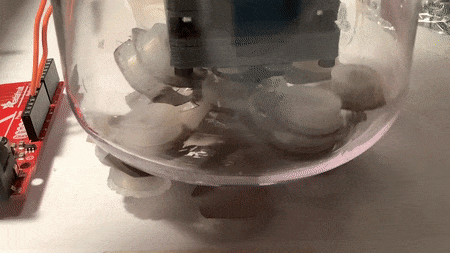
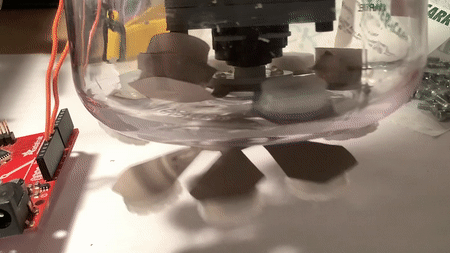
Read on for the rest of the method and discussion.
What you see here is as the servo is moving, the magnets on the petals are being attracted to the magnets on the servo block that attaches it to the rest of the assembly. There is some amount of force to keep the exterior magnets attached, sometimes.
We can see the petals problem closer here:
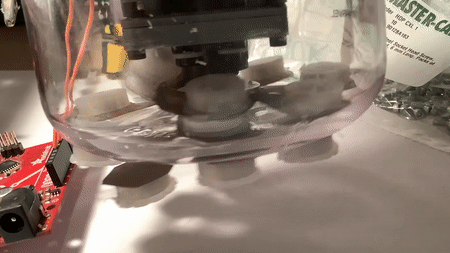
Because of this position error, after some time the material will rip:
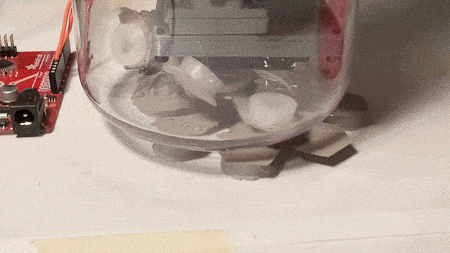
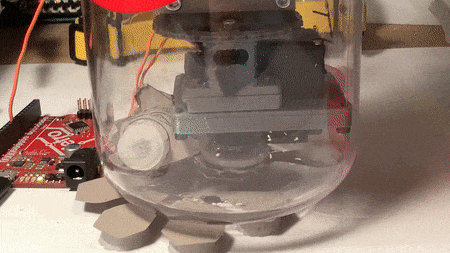
Although unexpected, the result does make sense. A different material could remove the risk of ripping. However, that would not address the problem that the holding force between the interior and exterior is weak.
The next experiment will use the taller, thereby stronger, magnets. The servo horn will only have 6 ‘petals’ on it, instead of 8.
There are other angles to be thinking about this problem:
- Could the magnets be attaching on the other face of the cylinder?
- Could it attach to a piece of metal, instead of to magnets? (Note, this might be tricky when keeping in mind the end environment (salt water)).
- A bunch of magnets that are on the servo horn, and the exterior magnets are stationary.
It will be interesting to try the next experiment. The pieces are done printing, so it should be a faster time to test now. The deadlines are now urgent: boxes of 3D printed pieces and the fasteners need to be sent to Tobi and Leo from my place on Tuesday if we want it to get there on time.
PS: You may notice that there’s a jump in log numbers. #08 is about more 3D printing, testing, design - including the onboard gateway enclosure and a spacer piece for the buoy. This will be written down later — the results of the experiment were more important.
Discussions
Become a Hackaday.io Member
Create an account to leave a comment. Already have an account? Log In.