INS-1 / ИНC-1
Fortunately, these single dot tubes are still easy to find in large quantity and rather cheap. Made by Gazotron, it seems they buildup a large stock at that time. The INS-1 has the advantage to be small and produce a nice dot due to the lens-style front. Plus its striking voltage is maximum 100V, lower than regular Nixies.
Procrastination
At first I imagined 5×7 dot character modules, such as the TIL305, but bigger. While playing and trying to make a tiny and simple 5V to 100V step-up power supply, I realized how simple it can be. Here we just need to reach the striking voltage and only 0.5mA. As there is yet non uniformity in brightness between tubes, no strong voltage accuracy is needed. Without the signal generator, it is a diode and a coil, shorted to ground with a transistor at high frequency.
Then comes the idea to mimic the popular serial cascading LEDs, such as the WS2812 or SK6812, the so called Adafruit ‘NeoPixel’.
Neon Pixel
What I observed when I was empirically select the components is one key parameter to reach 100V is low resistance coil and mosfet. The voltage can be adjusted by choosing the pulse frequency and width.
I was happy to see that only few pulses are needed to reach 100V. This enables pwm for bulb brightness control directly by driving the transistor. It is achieved with a pulse frequency of 100KHz and a PWM of 500Hz.
This leads me to the microcontroller choice. The peripherals needed are SPI, PWM, Timer, NCO and logic cell. The cheapest with all these options seems to be the PIC16F15313.
I first have issues with the SPI daily chain propagation delays. The data takes some time to be clocked out from input to output. If we use the same clock line for all the devices, the data will quickly be out of phase in respect to the clock.
A workaround is to delay the clock as well on each devices, and have in one side a data and clock in signal, and on the other side a data and clock out signal. Fortunately, this PIC has 4 logic cells, so I can use one to delay the clock, like a line buffer. I was lucky that the logic cell delay is almost the same as the SPI logic.
The only problem remaining is the rise and fall edge detection, they are apparently slightly different. It results a kind of clock pulse stretching, a change on the duty-cycle. However I can deal with it. With a clock speed of 480KHz, the 384th device is still receiving a usable clock signal.
Now that the prototype works, it is time for a PCB. The aim here is of course to have the smallest footprint, while keep connections at the opposite of the bulb.
I ordered the boards from OSHpark and JLCPCB. Both make very nice boards. OSHPark has the gold finish, and JLCPCB has the V-cut option, which is very convenient in my case.
https://oshpark.com/shared_projects/me17BntR
https://oshpark.com/shared_projects/xq9GWrM3
Lets start the long journey of soldering, The 2020 lock down gave me plenty of time to solder the 384 boards, on which there is 11 components.
A matrix
Meanwhile, it is time to think about a usable display. I then made matrix blocks of 8×8 pixels.
And controlled by an ESP32. I got the first encouraging result.
I start to make a support as well. A simple aluminium plate with two 3D printed legs. I add several slots in order to choose the inclination.
Coding
I’m using an ESP32, with the arduino framework, and the Platform.io IDE. The nice thing is I could extends the AdafruitGFX lib. So all the work of drawing, fonts etc, is yet done.
I added the notions of display size and buffer size. With a bigger buffer size, I can make easy scrolling by changing the coordinate of the view frame.
This Github repository contains the code and the schematics/PCB.
Conclusion
With around 20mA per pixel, at full brightness, the total of the 384 pixels is almost 8A. Everything is at 5V, so around 40 Watts is needed when all pixels fully on. Everything then is powered by a 10A 5V power supply.
This is the reason I’m keeping the display open, that way an airflow exists between the pixels and everything is kept below 40°C.
It is not the first matrix made of neon bulbs, here is a nice modular one made by Robin Sterling (@RC_sterling) :
And it is really big : https://twitter.com/RC_Sterling/status/1169707463215656960?s=20
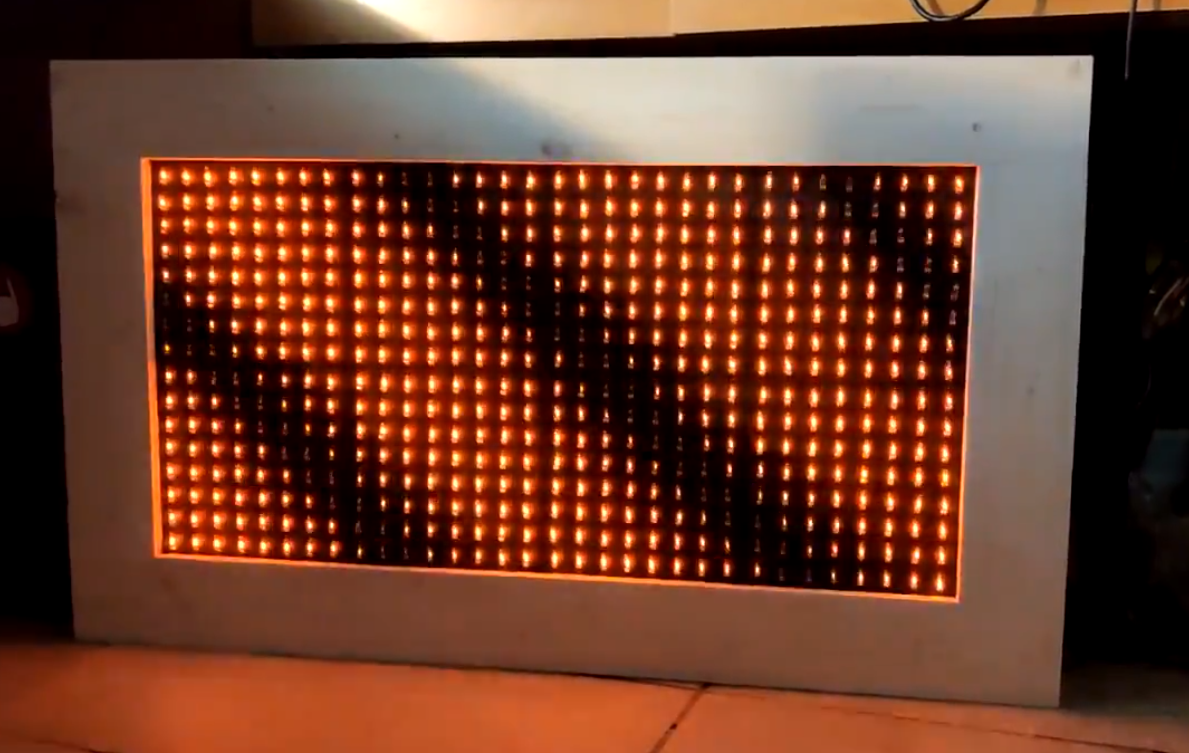
An other one by @cronos_sv spotted by dangerous prototype at Tokyo Maker Faire 2013:
I did not found much details, but there are videos here :
Recently Manawyrm Made 8x8 chainable matrices, featured in an atricle on hackaday:
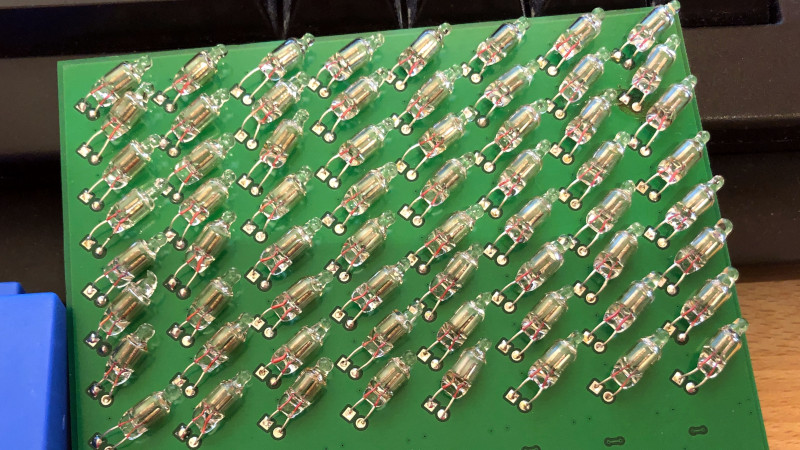