I've come into a few stepper motors, and have been scratching my head about how to connect something to them. You can buy pulleys, but you'll pay good money for any kind of metal collets. I hate paying more for a collet than just buying a new stepper motor.
I wanted to come up with three ways of using these (ubiquitous?) stepper motors that you may come across. 9These pictures just show tests of how to interface with the shaft, they still need a gear/pulley printed onto this thing to work for a mechanical contraption.)
Special Thanks to @madbodger on the adafruit discord channel for some inspiration.
Gear shaft motors
The most common types of stepper motors come with a pressed-on gear (left two motors in the top photo). I tried getting these gears off and they are STUCK. And in the end I realized that it may be best to take advantage of the gear.
To use these, I think it's best to print a press-on gear. For this, I measured the outer and inner diameter of the teeth and counted the teeth. I designed this with zero clearance and pressed it on, like this:
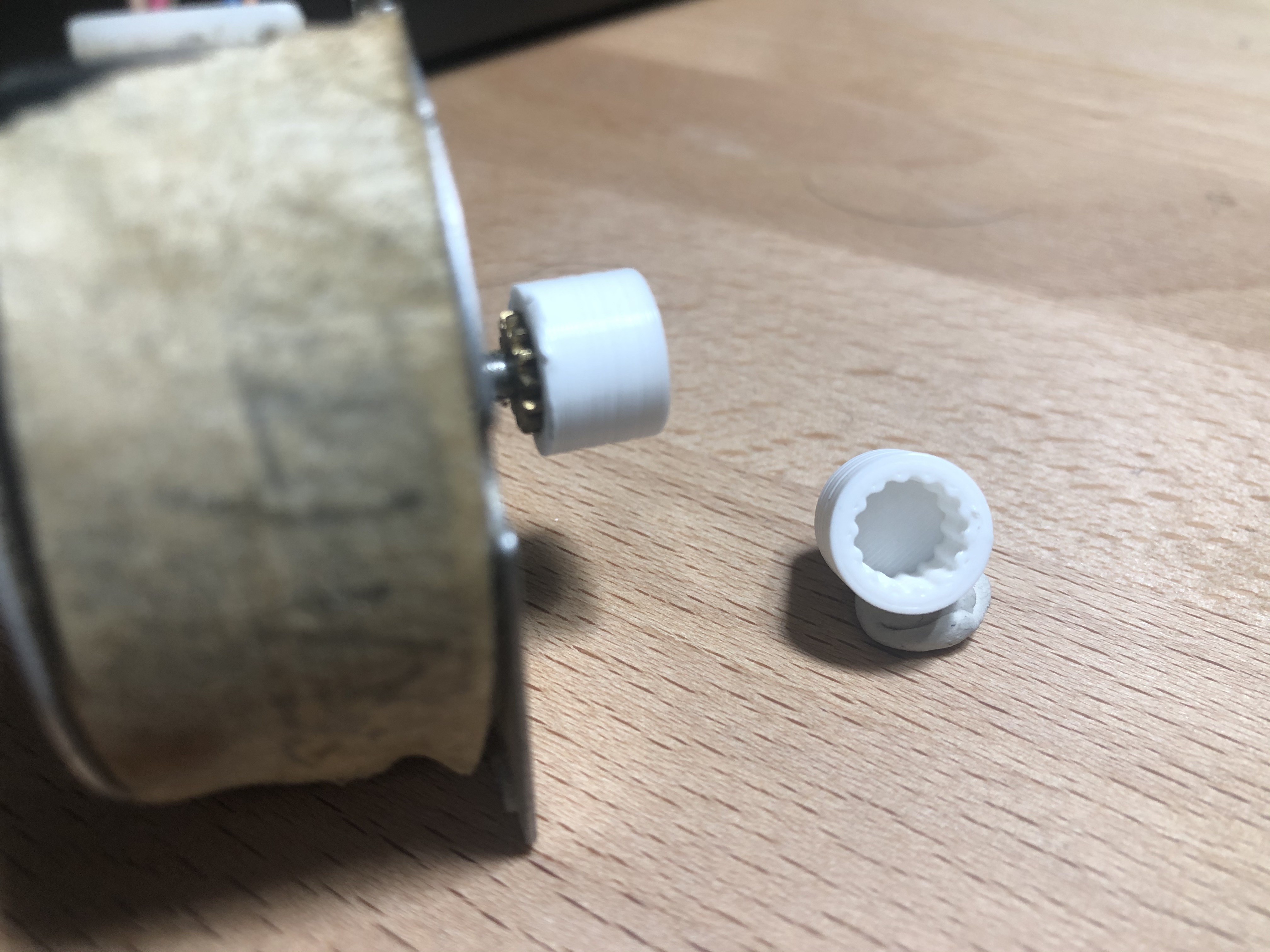
I have some stepper motors with beveled gears. I think it would work the same but you will need to taper the opening in the wheel.
If you design it with zero clearance, it will go on tight and be difficult to remove. If you look closely, you can see the screwdriver marks where it took a lot of effort to get it off and I deformed the edge. It was a little looser the second time I put it on, but it still was not going to spin. I think this is the best approach for geared shaft steppers.
Smooth shaft steppers: 3-Bolt and 1-Bolt options
If you have smooth shafted steppers, I've seen clamp-stype metal collets or collets with set screws. I'm suspicious of those, so I designed a couple of collet-like structures. The first uses three (3) quantity of M2 bolts to keep the 3D printed layers in compression.
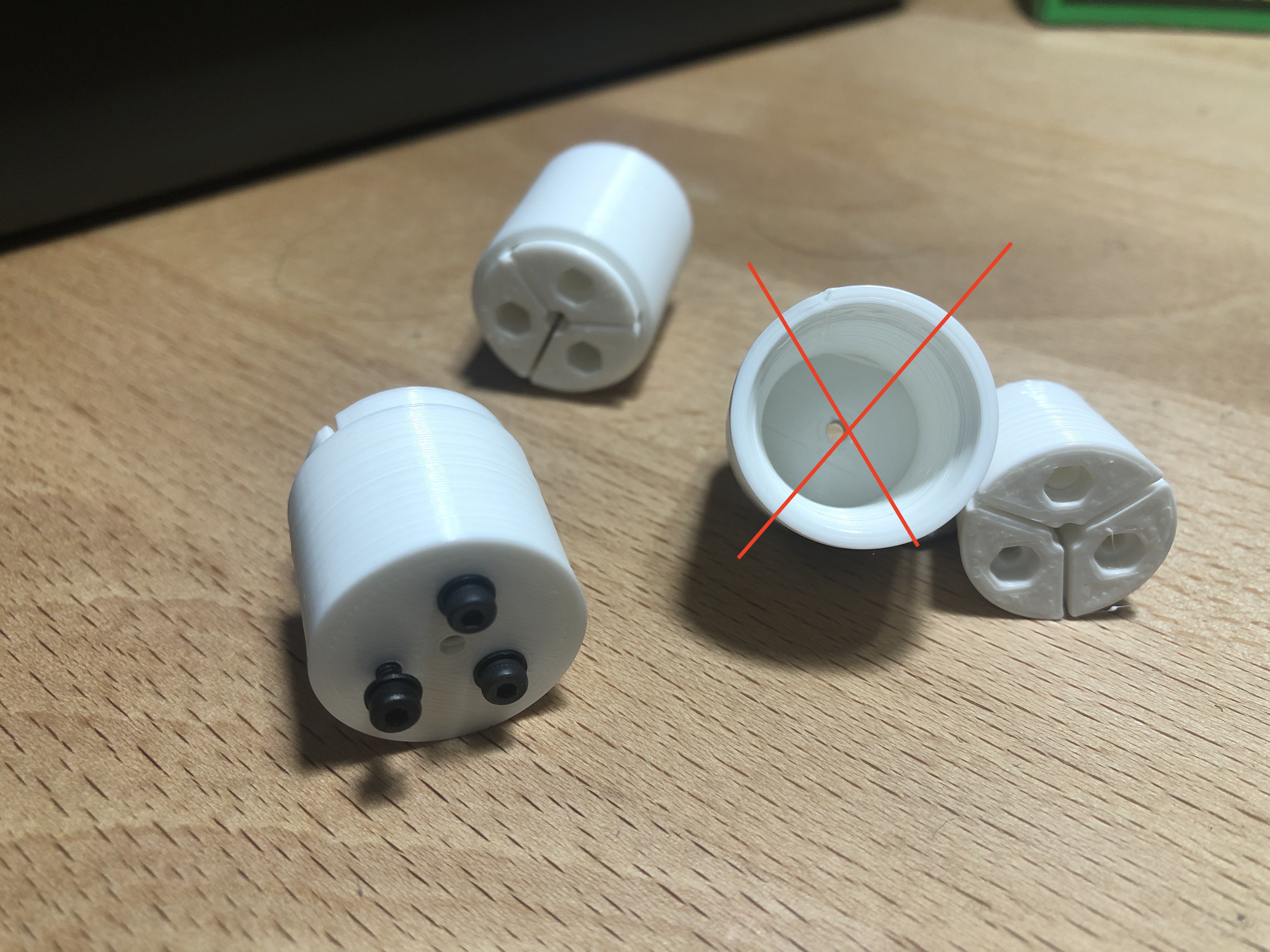
In fact, I tried several times to make this with one bolt and failed since the layers ripped apart:
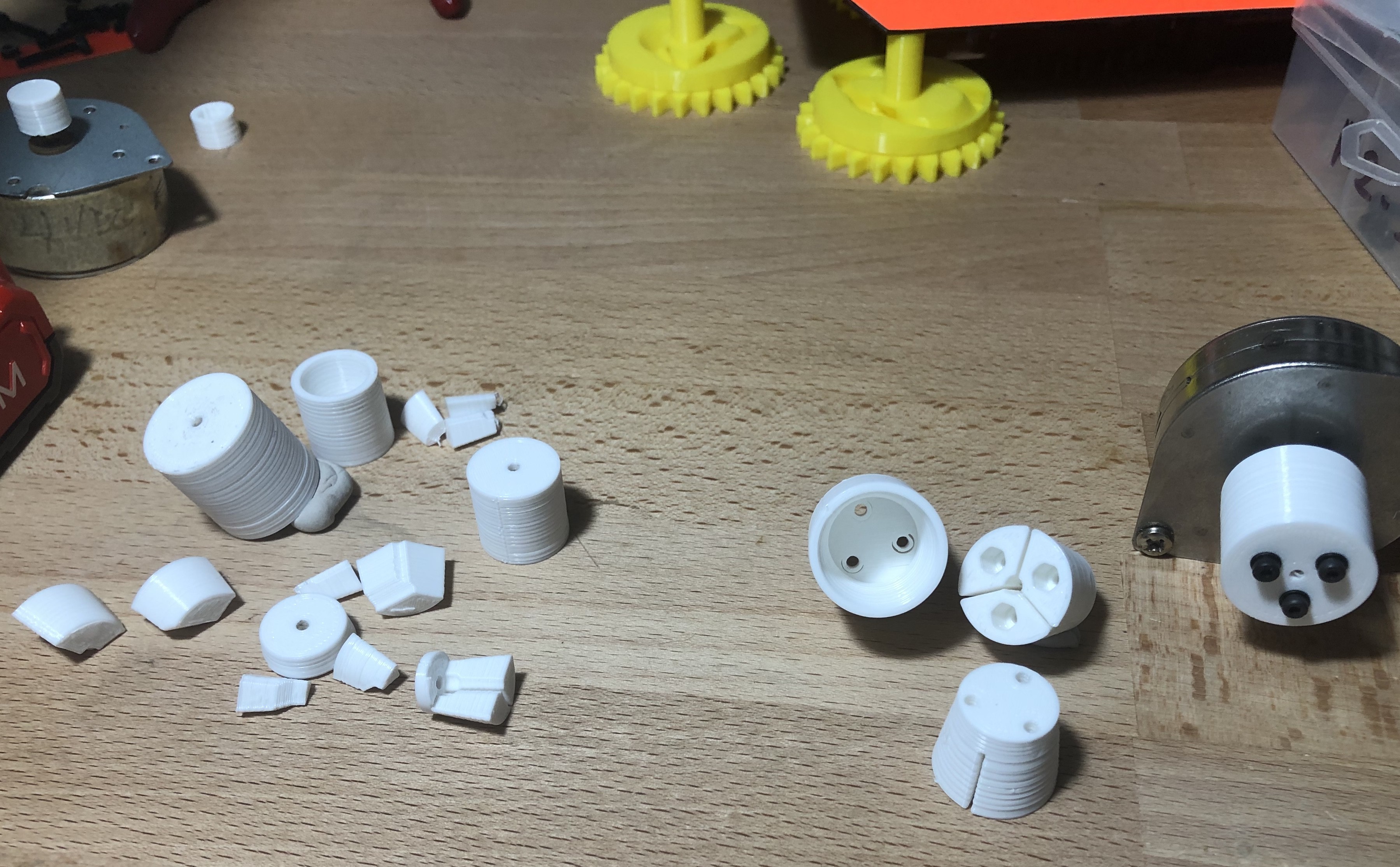
That's why I gravitated to use the three bolt version, since the bolts and nuts compress the layers to prevent them from ripping apart.
1-Bolt version
As never one to be deterred, I wanted to reduce the number of bolts so I got inspiration from this collet design by b3n3d1k7. For this collet is 3D printed with two flats to Make it easier to print. Here is my version with a single M2 bolt and nut. The nut fits into a slot on the side since it is printed with the “side” down on the printer, the bolt doesn’t tend to rip it apart.
I prefer this last version for smooth shafted motors. I would never use this where something important depended upon it, but this would probably work for a lot of cases. I haven’t tested the torque capability of these but my finger testing says these will probably meet many light duty stepper motor needs. Now all you have to do is design the gear/pulley to go onto here and the rest of your mechanical marvel.
Let me know what other ideas y’all have used that work and ways that fail brilliantly in new and interesting ways.
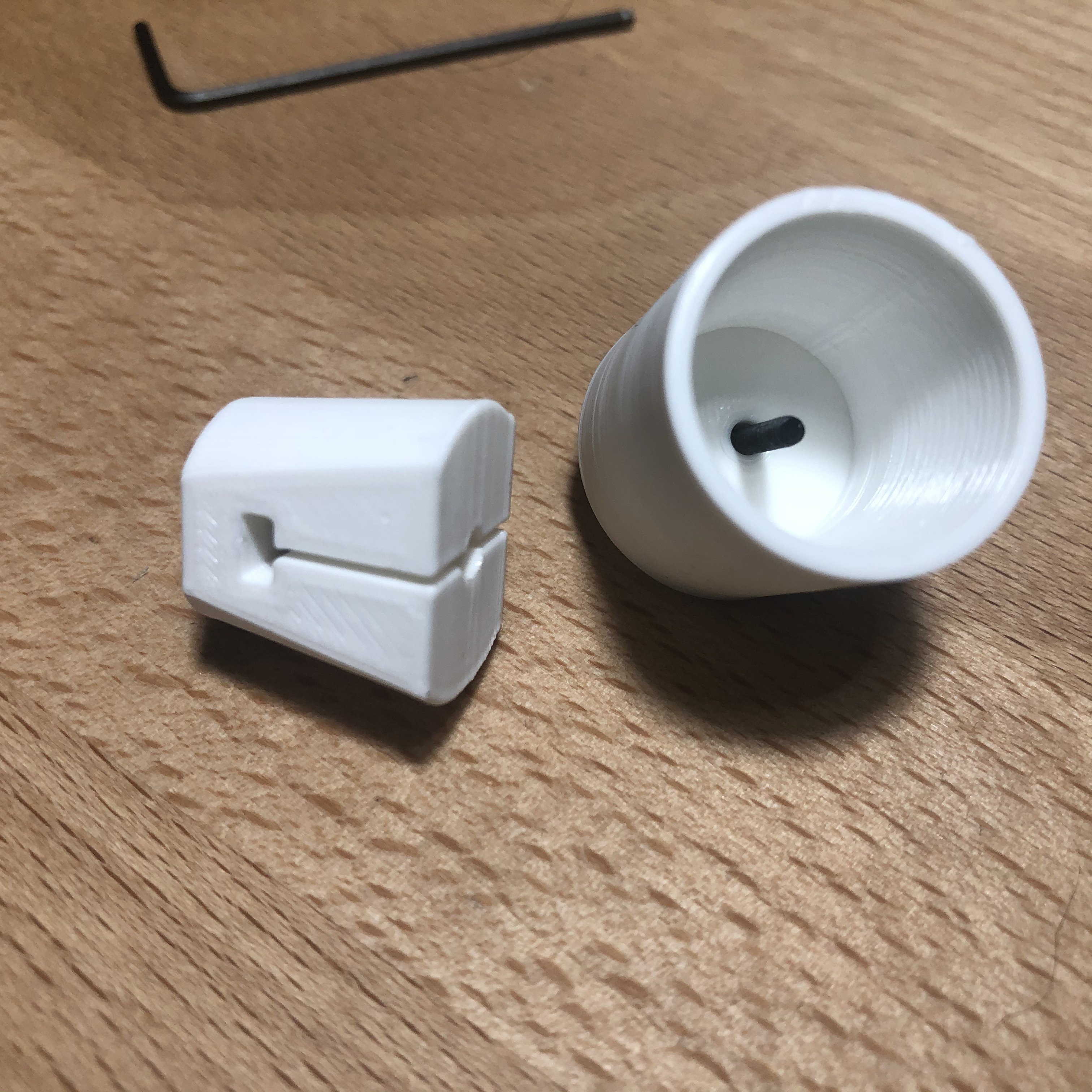
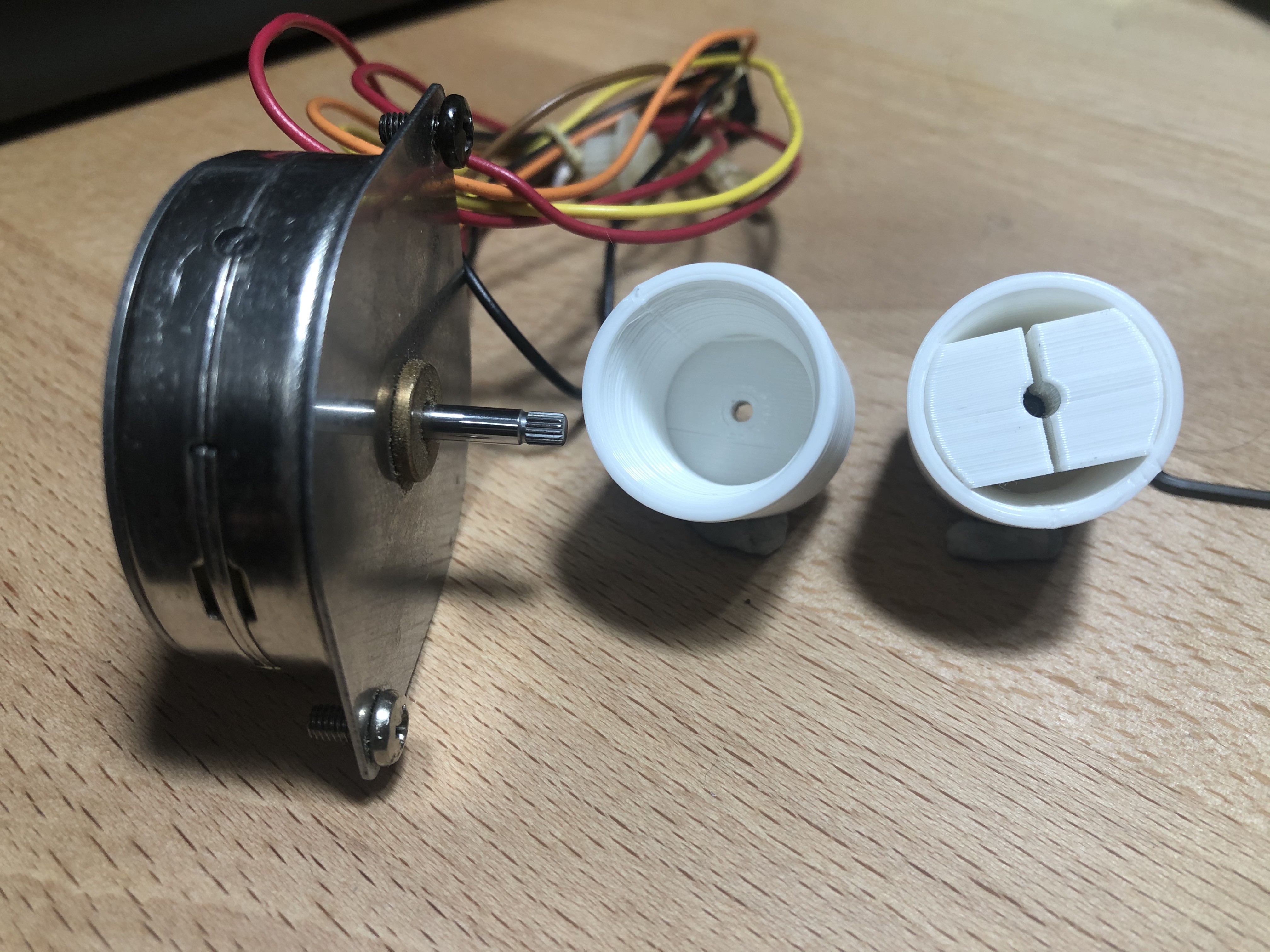
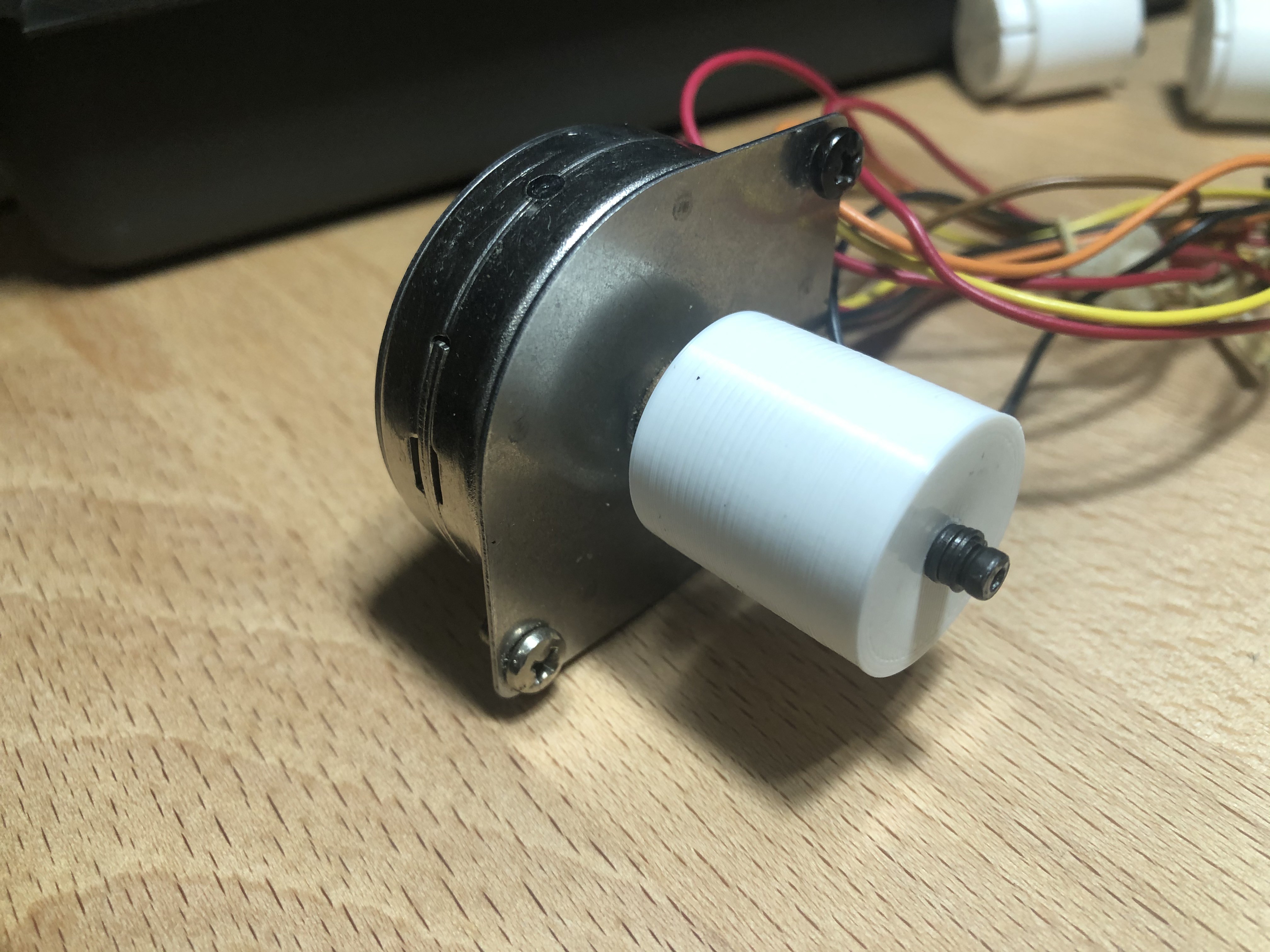
Hi KM98 Kudos to your skill and ingenuity with 3DP. Elegant 2 piece collet must surely find a worthy application. IMHO however, its a sledge hammer to crack a nut. Conventionally a smooth shaft has a flat on it allowing the use of a bush with a grub screw eg a vol control knob etc. You can easily grind a suitable flat on an existing shaft job done