I added a mains powered heated bed because the prints weren't sticking well to the print plate, so this step couldn't wait.
Then the printer got an on/off switch and a cold-appliance(power) connector on the back. The connector replaces the red power cord that was attached directly to the printer, as seen in the time-lapse video of the last log.
Idea: magnetic bowden coupler
The redesign should incorporate two 40mmx10mm fans, a Bltouch sensor and a new folding mechanism for the bowden tube.
I came across this magnetic bowden connector and thought that if somebody sold this, it might be a feasible way to get the bowden tube detachable. With the use of CNC Kitchen's data from his extruder comparison video I knew how much force an extruder would generate, usually no more than 100N. With this information I started looking for suitable magnets that can hold more than 10kg of weight. I settled on N52 12mmx3mm cylindrical neodymium magnets, each capable of holding up to 3,1kg. I planned to use four of them, for a total holding power of 12.4kg.
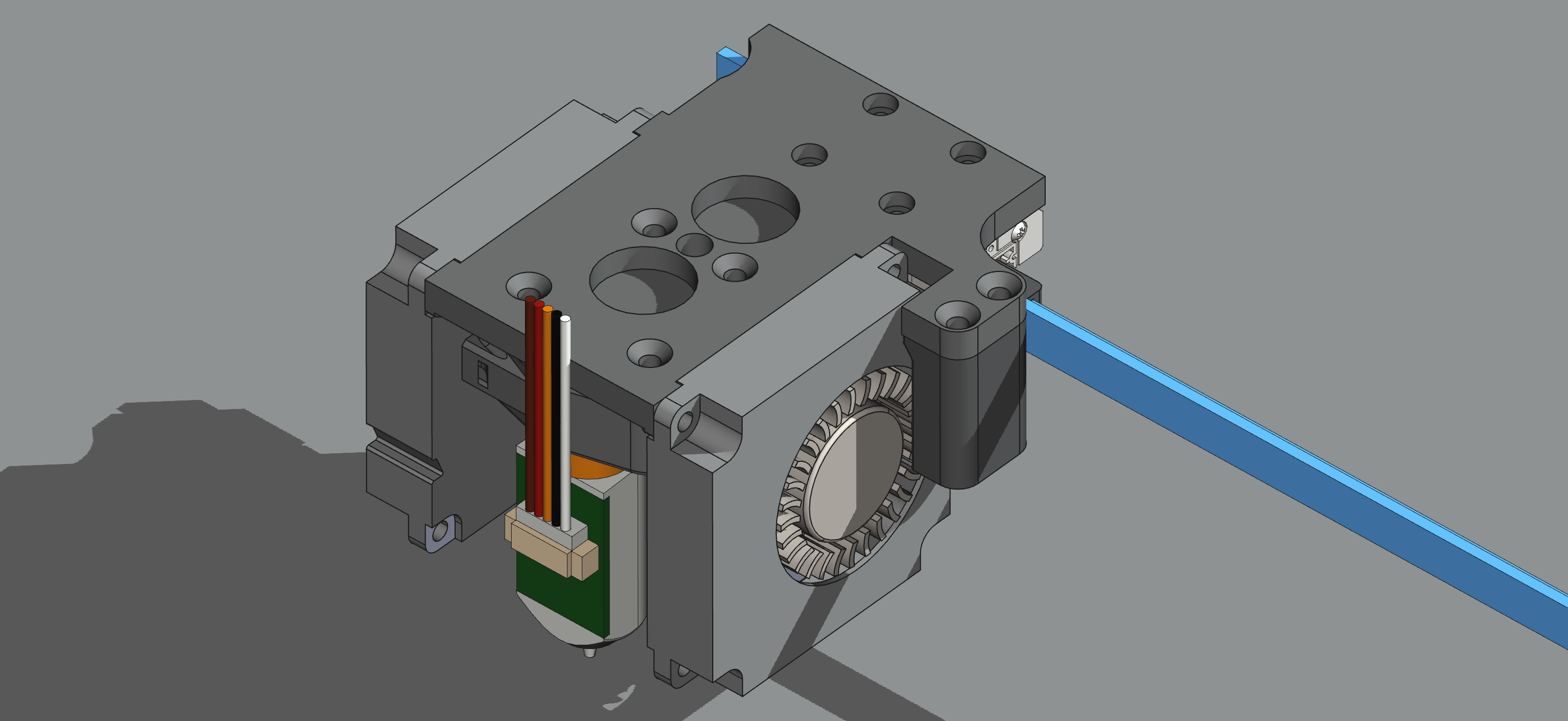
I only have this picture where you can see the one part of the printhead and the bowden tube holder that can be attached to the printhead through the magnets.
The concept with the magnets had several problems:
The magnetic bowden coupler held together during normal printing in the centre of the print bed, but when the printer moved to the corners of the print area, the coupling broke due to drag on the bowden tube.
In addition, the magnets, or rather their strong magnetic fields had severe effects on other components of the printhead. The Bltouch sensor couldn't be placed near the magnets because it wouldn't work properly. The magnetic fields of the magnets inhibit the lifting motion of its tip.
Secondly, the magnets slowed down all of the fans. The part cooling fans sometimes stopped spinning or didn't start to spin. Which surprised me quiet a bit because I thought the fans were far enough away from the magnets. Anyway, for these reasons I had to abandon the magnetic bowden tube coupler concept as it was too weak and caused other components to malfunction.
I think it might work if the magnets are stronger and further away from the other components. But the Xprinter's printhead needs to be very small, so the relatively close placement of the printhead's components is inevitable.
Discussions
Become a Hackaday.io Member
Create an account to leave a comment. Already have an account? Log In.
You should look at using a 90 degree hot end from the Positron project. I believe Phaetus is working on producing one, and potentially combine it with their APUS extruder.
Are you sure? yes | no
A Halbach array of magnets could make the mating-side stronger whilst reducing the mangetic fields emitted from the other side.
Are you sure? yes | no
Oh, so that's called a "cold appliance" connector. That lead, indirectly, to some useful information about a current puzzle. I wonder what distinction is implied by "cold". Searching for "hot appliance connector" doesn't help.
edit: found c13/c14 vs c15/c16.
---
Maybe the magnet idea can be saved. I don't know much about magnets so caveat lector. A magnet in a steel (iron) cup pulls harder than a bare magnet. and the attraction is directional with little strength behind/outside the cup. You can get either "cup magnets" or cups for your magnets, and matching washers for a favorable opposite surface (if not using a second magnet). So maybe you can get sufficiently strong attachment with fewer magnets and less stray field.
Also I wonder if a pin/hole constraint to limit rocking the connector would keep the connection near enough within range of attraction even if a free-fit constraint still rocks a little.
It looks like magnet cups and washers typically have a countersink for a flat head screw in the middle. e.g. https://www.kjmagnetics.com/products.asp?cat=161 . And it looks like the main difference between a "cup magnet" and a magnet in a cup is that the cup magnet has the countersunk hole through the whole unit. Otherwise the installation becomes permanent when you drop a magnet into a cup and cover the screw in the bottom of the cup.
Also: some shielded speakers, for example, use an opposed "bucking magnet" behind the working magnet to reduce the field outside the driver. All I could find about that is that people say it's not trivial to do right and the bucking magnet is usually smaller diameter than the main magnet.
Are you sure? yes | no
Thanks for the hint to the cup magnets, I had no idea that these magnets with the countersunk holes had this particular property. At the moment, the bowden tupe is attached to the head with a mechanical clamping mechanism, which works reasonably well. Getting a greater holding force and less stray field with these cups sounds actually great, so this is a good idea for the future.
Are you sure? yes | no
You're welcome :) Looking forward to seeing your further progress with this idea.
Are you sure? yes | no
Just found what looks like some better-than-average info: https://sourcemagnets.com/products/pot-magnet/
e.g. top of page pic shows an example of {more steel / less magnet} giving the same useful field with less stray field than (more magnet / less steel} in the same overall dimension.
Are you sure? yes | no