tl;dr: if you can see it you can tweak it
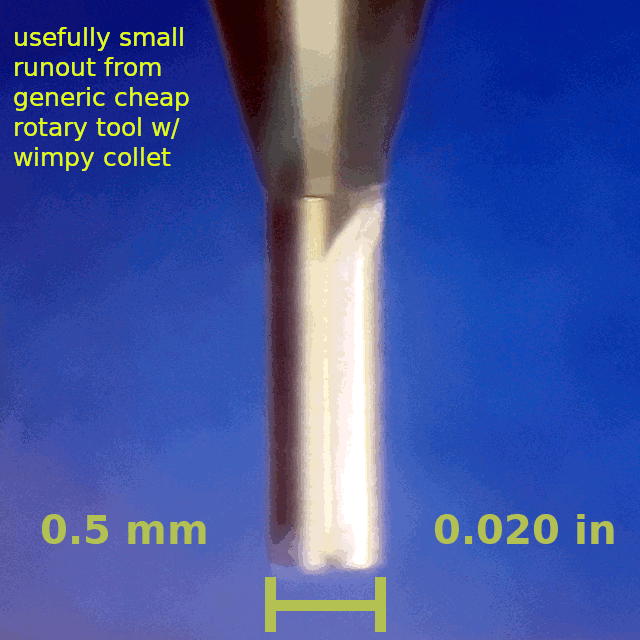
Some examples of work from this little CNC and its precursor demonstrate pretty small runout from a generic faux-Dremel rotary tool. Repeating that will be part of replicating this project for anyone so inclined. It also seems like it could be useful to anyone trying to do fine work with a not-so-fine tool.
The point, when I get to it, will be anticlimactic. It's pretty simple. But I haven't seen it elsewhere in my limited scope of reading. So: sharing. Akshully I've written this before but that was buried in another topic and without illustration. So: sharing with pictures this time.
To reduce runout when using a cheap generic rotary tool and maybe some other small-cutter tools:
- See the current runout using stable magnification that you're not trying to hold still in your hand
- Tweak the bit toward center
- Repeat until runout sufficiently reduced
That's all <yawn/>.
More verbosely, and with pictures...
See
The gif above shows a view through a microscope on a stand that can look sideways. But that's cheating. Here's a method more in line with the "low cost" theme here:
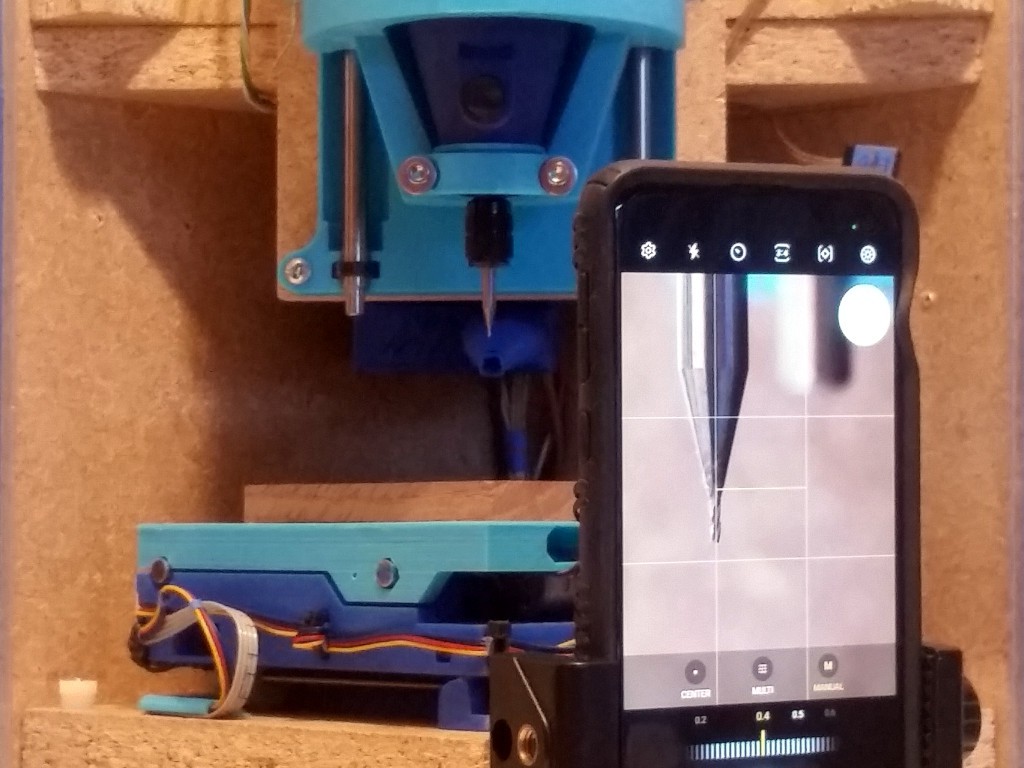
That's my daily driver phone in a little pocket tripod (which I've cropped :/ but you've seen a tripod before).
- that phone is not new but not too old to have a camera that can focus close enough to do this
- manual focus in "pro" mode helps; otherwise you'll probably need to put something right behind the bit to appease the autofocus
- the viewfinder grid provides a fixed reference to help perceive small deviations at the tool tip; otherwise put something with a vertical edge close behind the tool (which might also appease the autofocus if you're stuck with that)
That looks like this:
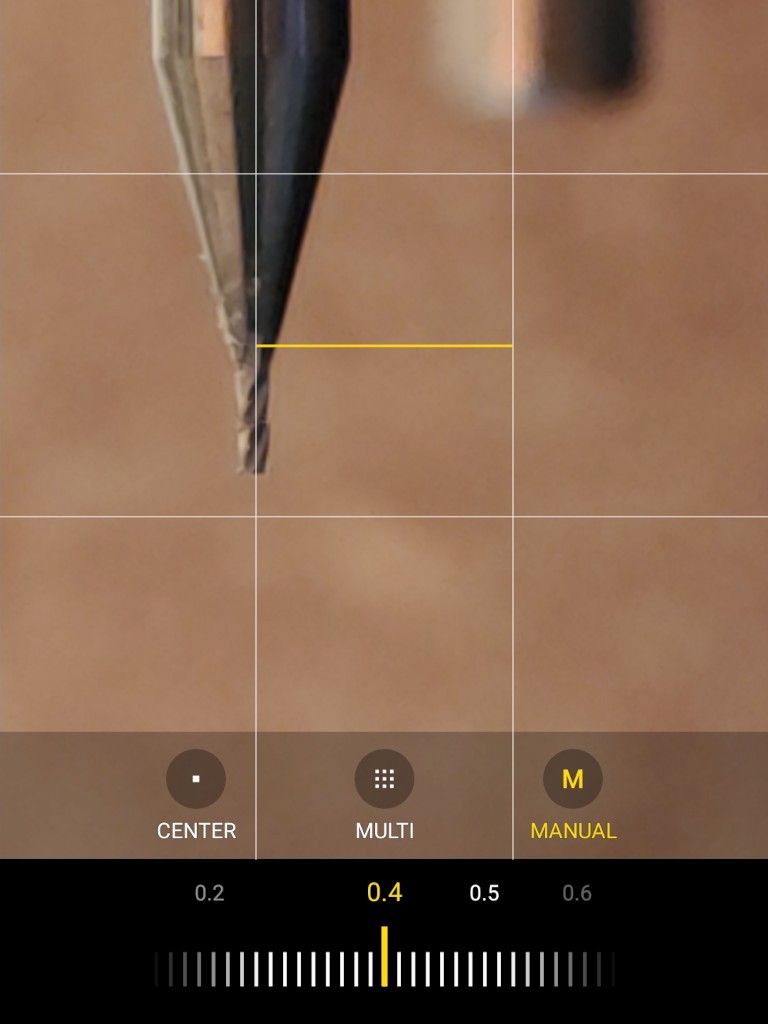
While less crisp than the gif above, you can see that you can visually resolve a small fraction of the bit diameter (0.5 mm in this case), which is the practical scale for runout.
Tweak
Established Brand general purpose rotary tool collets aren't fantasticly precise. Generic clone rotary tool collets are really poor (typically, in 2023Q4). They are basically poorly made ball joints. The good part of that is you can point the bit any direction you want.
I'm using very small cutters here, which don't generate very large radial forces. So firmly finger tight on the collet is tight enough. A very tight collet makes it hard to make small tweaks. If the collet is not tight enough, the bit will "walk" out and drive down into the workpiece. So there's an element of "just right", but for small cutters that seems to be a pretty wide range and easy to hit.
Very small cutters break easily at the tip, so take care to apply tweaking to the shank and not the thin end.
I think you should probably not do this: I started out tweaking by hand -- with a finger around the bit and thumb against the collet for good leverage. That sometimes meant pulling pretty far down the narrowing neck of a short bit and perilously close to the skinny end. Nothing bad happened, but that just seemed way too close to blood to expect that it would never go badly. So I printed a tool:
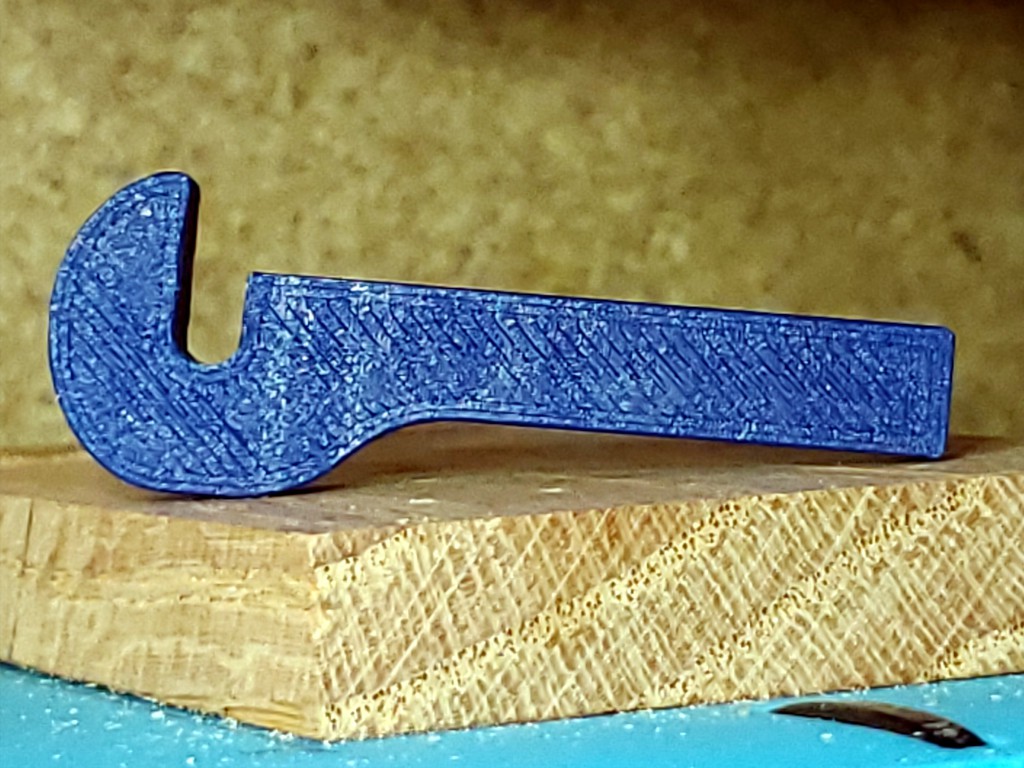
I've been using that, but It's just a first whack at the idea and not a great example. So I hope you'll make a better one.
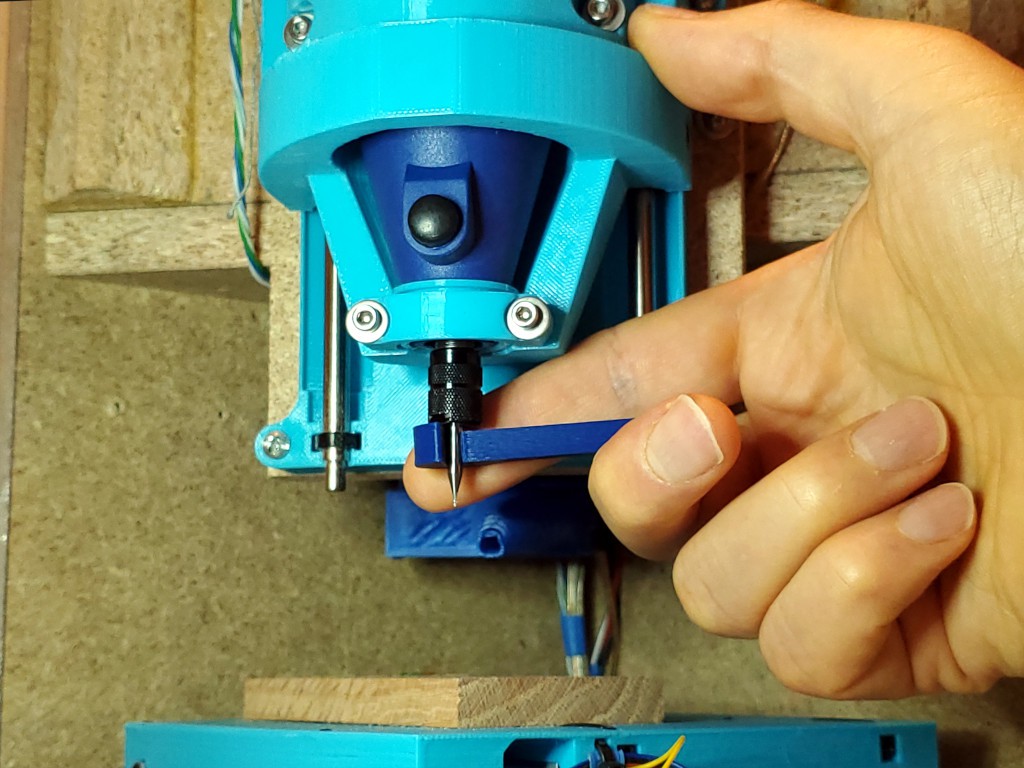
Applying tweak without slashing a finger. In the photo my finger is behind the bit for contrast, which makes this a poor example of applying tweak without slashing a finger, but you can see the idea.
Repeat
While you probably won't get as close as you want on the first try, this method seems to converge much faster than "open loop" fiddling for that once-in-many low-runout chuck-up that teases you with knowledge that it's possible but only happens when you're not trying to make it happen rant rant.
And if you're still reading...
Rolling a stiff cylinder around the collet nut to make a slip-on anti-pointy guard has saved some bits and probably some blood. Especially useful when I want to leave a good set-up in the collet while not really paying attention anymore.
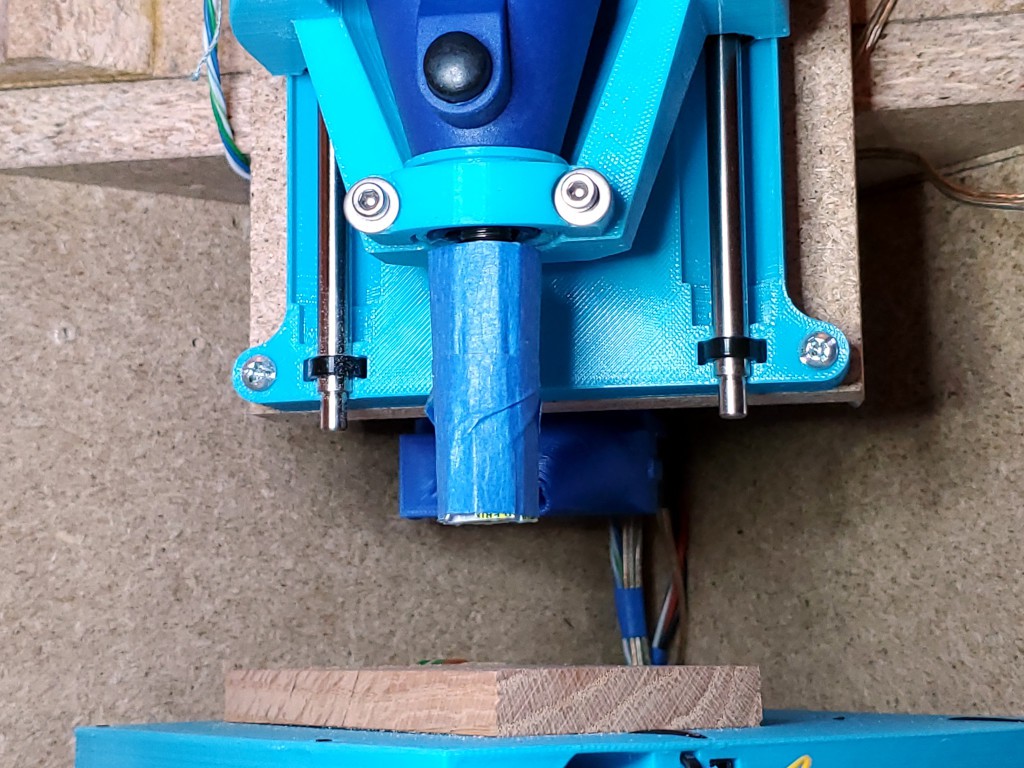
Coroplast (abundant free supply: election signs) flexes in one direction for easy wrapping (I probably cut some slits in one side, maybe, I think) while maintaining stiffness lengthwise.
Discussions
Become a Hackaday.io Member
Create an account to leave a comment. Already have an account? Log In.