This doors thing has been going on for a while. I think the latest try is at least good enough to stop thinking about for a while.
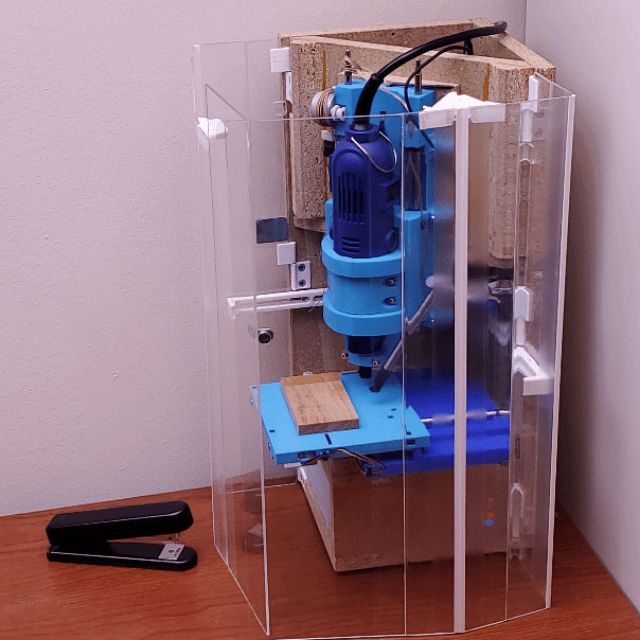
the main things
- "real" hinges that are not bulky
- long sides held flat without loose parts or awkward closure
- other bits done better
"real" hinges that are not bulky
Early iterations used clear packing tape for hinges. That makes nearly perfect hinges.
but...
Packing tape, especially the adhesive, doesn't last forever, especially when exposed to light. And it's not really "real" from a product design/manufacturing perspective. Why do I care about "real"? I'm not planning to get into manufacturing or long-term product support, but as I was continuing to spend time on this idea it seemed less attractive to commit so hard to a design element that could never be made "real". That, and some conversation at MRRF last year. After looking at a bunch of worse options, I tried a "living hinge" extrusion. That was "real" but really bulky and much less nearly perfect. Meh. Then I found some coextruded acrylic+flexure hinge that is "real" and not bulky.
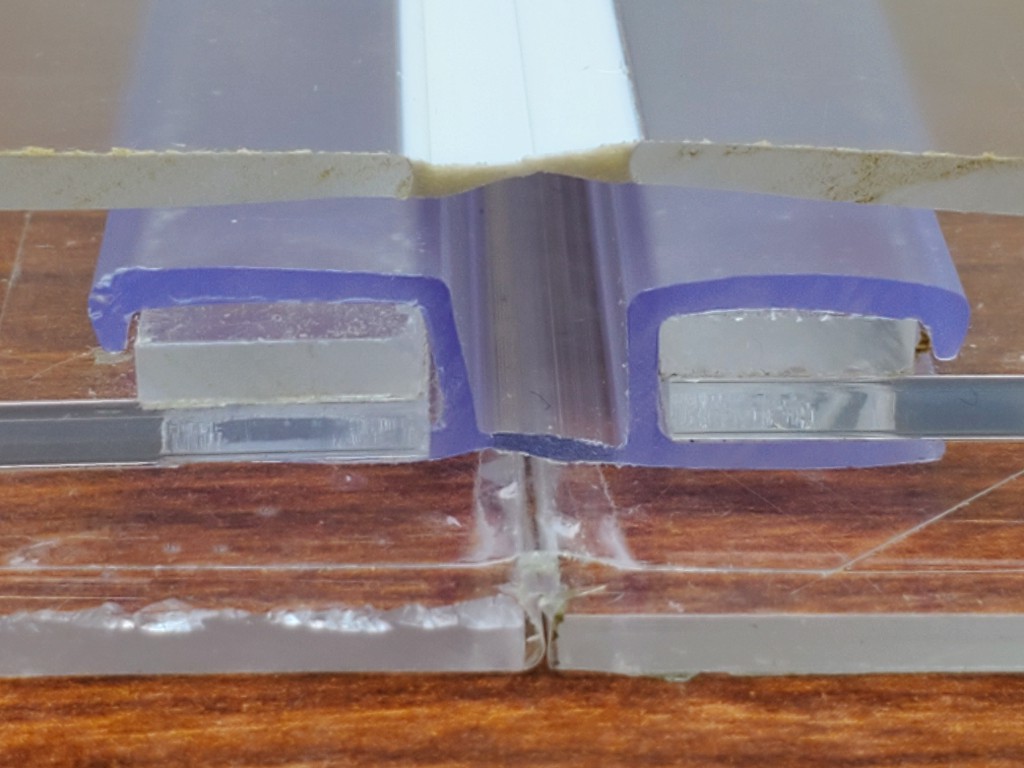
And the not-bulky hinge was also close to the same thickness as the ~2mm acrylic I've used for recent iterations. And I've read that near-perfect butt joints can be made between acrylic sheets with the right chemistry. For this build I taped the butt joints, but they could be real...
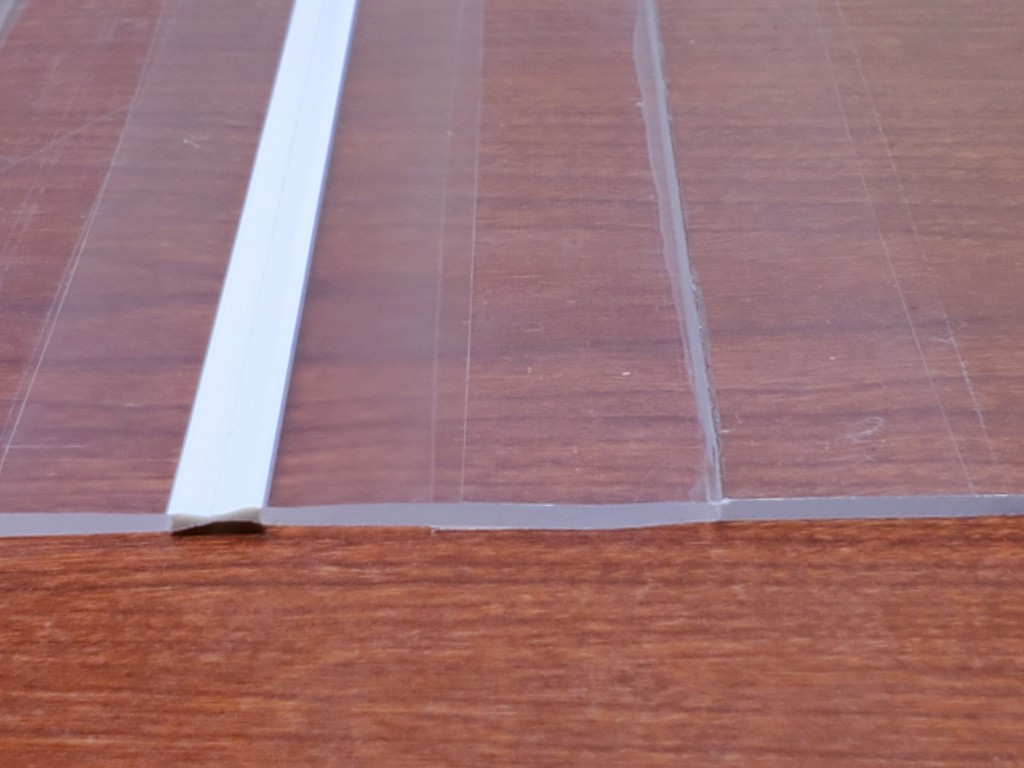
These hinges can fold 180° flat, but leaving them for long periods like that seems like it would be hard on the material -- especially if the outside of that fold is an edge exposed to abuse. So I kept the overlapping 90° folds around the corner as adopted for the bulky hinges instead of going back to the 180° flat folds on each side like what I took to MRRF last year.
(I haven't re-found where I got the tape-hinge idea, but did find that RC foamy plane builders use various kinds of tape for hinges in a similar way.)
that's great. but...
The coextruded hinges are unobtainium at retail. And I don't want to dox my source.
so...
Having thus determined that "real" no-bulk hinges are possible, I'll probably go back to tape for future iterations. Maybe there are tape options that could pass for "real". UV resistant? There is "hinge tape" for books, etc, which might work, but this isn't quite exactly the same as taping up a library book. ?.
long sides held flat(-ish) without loose parts or awkward closure
In this corner-oriented version of the frame, the doors fold up compactly for storage by folding where they're not supposed to fold in operation. Then they're supposed to not fold (much) where they're not supposed to fold in operation. This seems to work ok:
For a first try I made some metal clips that slide along the top edges of the doors to lock out the "wrong" joint.
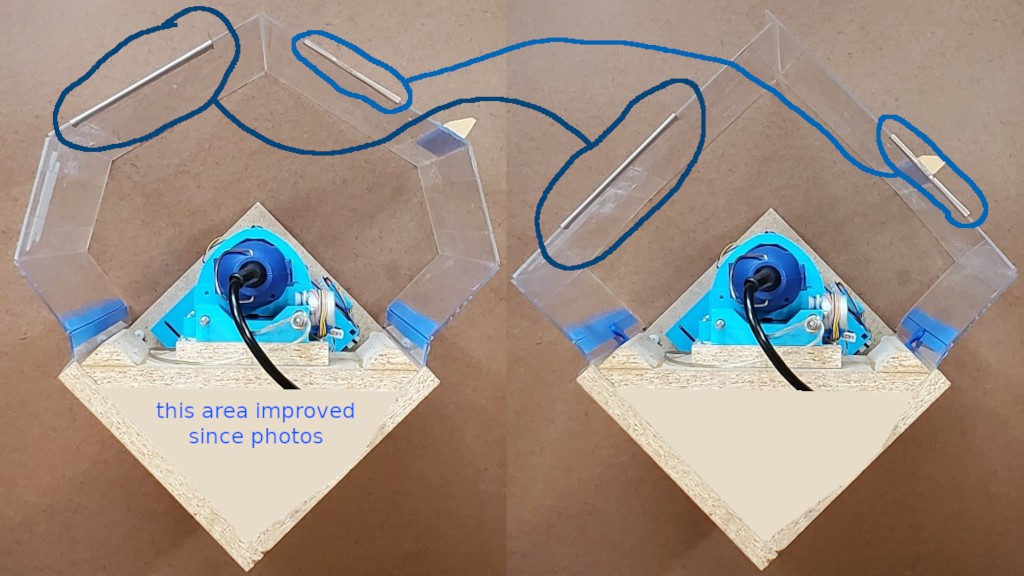
That kinda worked, but:
- separate parts = lost parts
- (some variation of pin-in-slot might have worked but didn't have any great idea how to make that simple)
- changing from 180° to 90° folds for storage (because bulky hinges) would have put one of those on the outside where it would be vulnerable
When the sides are straight, the two doors meet at a perpendicular corner. Instead of enforcing straight sides, I also considered enforcing perpendicularity where the two doors meet, which would force the sides straight (if the short sides were held out straight from the frame sides). Using a closure that could attach only to the outside surfaces of the doors because of how the doors fold closed. I had an idea for that sketched that I think would have been not too complicated to make, but didn't get that done before changing how the doors fold.
Changing to the "real" but bulky hinges changed how the doors fold, which:
- would have made one of the top-edge clips vulnerable on the outside of the closed-up box, and
- allowed closure parts to attach to the inside surfaces of the doors instead of only the outside.
So I changed over to enforcing perpendicularity at the corner with a rigid magnetic closure instead of straightness at the sides.
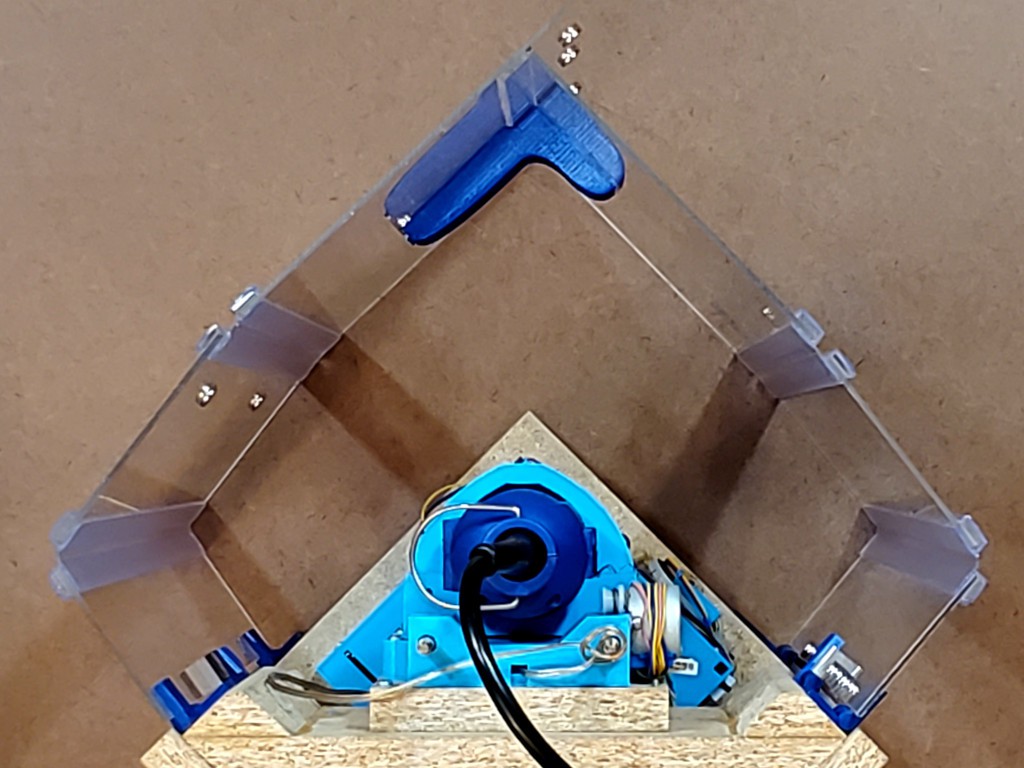
When I started remaking the doors this time around I assumed I'd be repeating the ⟂ closure with incremental improvement. While having a little rethink before actually cutting stuff, and thinking I could do something on the inside of one door but only one, some recognition filtered through my head that it wouldn't be unthinkably horrible to cut down part of one of the doors a little to expose the inner side of the other/outer door when closed up for storage. Then I could do something about locking out the "wrong" hinge from the inside. After some hours of leaning on constraint-solving parametric CAD, and cutting the "inside" hinge down more than necessary after cracking it on the first try, this seemed to work ok:
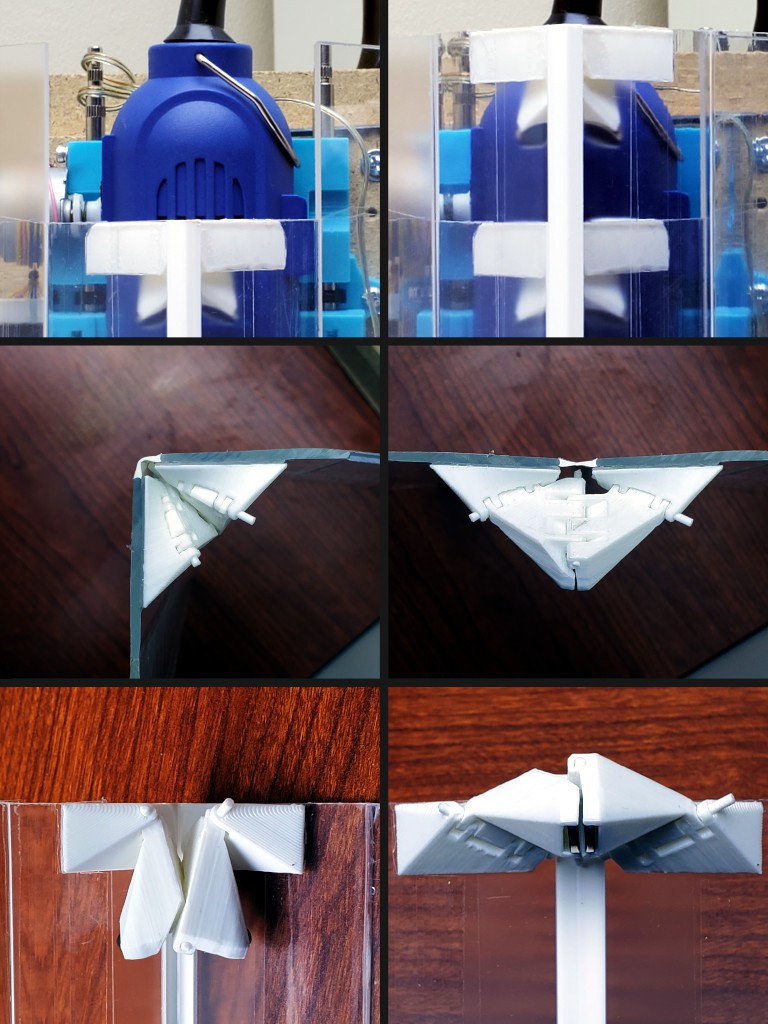
mid: hinges lock when opened slightly beyond 180° flat (2nd unit printed overshoots flat at top to counter twist down thin panel)
bottom: magnets self-lock when opened; light bump "breaks" lock to close up for storage
(yes, the hinge pins need trimming -- and maybe a little heat-squish to secure)
That holds the long sides of the enclosure straight(ish) without extra loose parts or extra bulk/complexity in the corner closure. Yay. It wasn't the main problem to solve in this iteration (hinge bulk), but I think it seems like a good thing to have these hinges solve themselves when (vocab? "open"/"close" is ambiguous here) deploying the enclosure for operation and require just a bump each when stowing the enclosure for storage, instead of adding bulk and tedium to every open/close of the corner closure while in use.
other bits done better
- magnetic closures greatly simplified for both storage and operation
- better slide-out braces for the short sides (earlier parts designed for similar but different function)
- less bulky but still removable hinges
- lift-off hinges more positively locked in place when closed
a little more about the lift-off hinges
This iteration was mostly driven by the flex hinges between panels.
The hinge between the frame and first door panel was also taped in various ways in iterations until the prior build with the big extruded flex hinges. Then the bigness of the extruded flex hinges gave some "free" thickness to fit a mechanical hinge at the frame. After looking at a bunch of hardware, I modeled and printed some pintle+gudgeon hinges that worked ok, and provided an extremely simple way to remove/install the doors. That was enabled by a stash of short 3mm dowel pins acquired for another project (that may yet turn up in this wee CNC context...), with the downside of adding a specialty part to the BoM mitigated by the relative generality of the pins vs some particular mechanical hinge.
For this iteration, I liked the idea of the lift-off hinges, but didn't have the "free" room for them to be big. So:
- made them thinner - which required thinner walls around the pins than I would have thought prudent, but trial parts seemed ok and finished parts have held up ok so far. The gudgeons are small targets for drop-in fitment, so I tried to finesse the little material there is (~1mm around around the pin less free-fit clearance) so that I can just stab a door into its home corner in the frame and the gudgeon shape will capture the pin as it slides down the corner. It works pretty well and hanging the doors is easy.
- recessed a couple into the frame (2 of 6) - after hesitating to add complexity and more tools to making a frame/box before remembering that the project intrinsically implies possession of a rotary tool, and I had a very inexpensive & small depth-setting widget:
Discussions
Become a Hackaday.io Member
Create an account to leave a comment. Already have an account? Log In.