There seems to be a need for stand-alone step-up and step-down DC/DC converters in Radio Controlled aircraft. I'm thinking about possibly making a long range quad copter that runs on a single Li-Ion 18650 battery. Unfortunately, most FPV cameras and video transmitters can't operate much below 5VDC or 3.3VDC, whereas the battery can drop to 2.5V before it is exhausted.
Step Down (Buck) Converter:
I was watching a YouTube video where a guy was using a step down converter to power a GPS unit separately from the flight controller power supply of a quad copter in order to acquire satellites faster and get a lock. He uses an iFlight Micro BEC to step down the battery voltage (8-25V) to the 5VDC required to power the GPS. (BTW: the GPS only draws about 50mA @ 5VDC.) The Micro BEC dimensions are 14mm x 11mm x 1mm, and it weighs 0.8g. It's not cheap.
I went to AliExpress to see what was available in the same category and purchased a lot of 5 3A DC/DC step down converters for $0.28, with $6 shipping from the U.S. These units have dimensions of 17mm x 11mm x 4mm. It weighs about 1.5g without wires. They arrived pretty quickly and I verified their functionality and parametrics. I replaced the potentiometer on one unit with a 36k resistor to get 4.97VDC output. The unit has an overtemperature shutdown that kicks in around 1.8A -- it shuts off the output, cools down, and turns the output back on. A practical upper limit of continuous current is probably around 1.5A, with short bursts above that. I did take some efficiency data at one load current point:
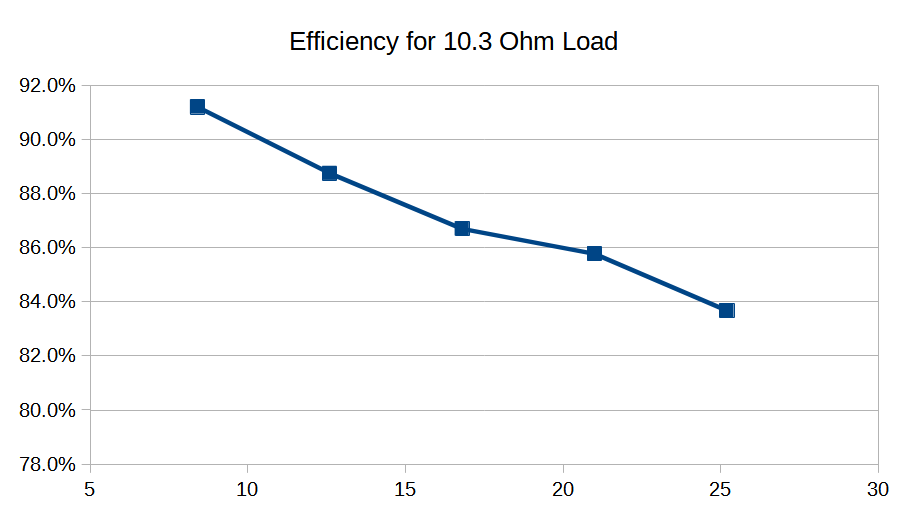
I also designed my own buck converter, just to see what was involved and if I could make something smaller and lighter.
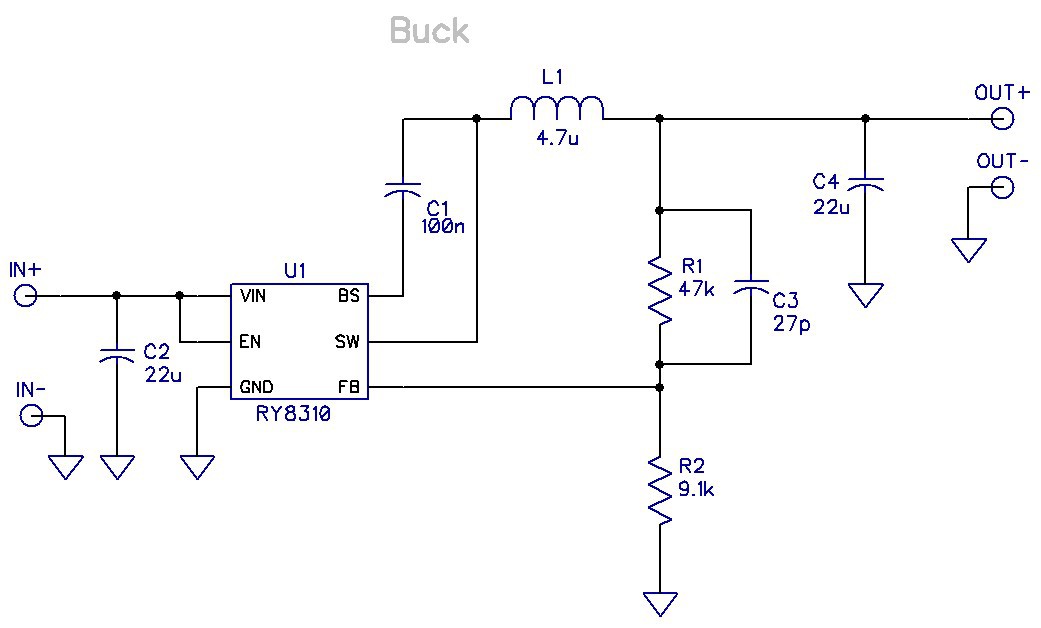
All of the components came from my current inventory: 0805 caps, 0603 resistors, 2x1.6mm inductor, and the RY8310 is a SOT23-6 package. The Rychip RY8310 is a 1.4MHz synchronous buck, with input voltage limits of 4-30V and 1.5A peak current output . The inductor is a VLS201612HBX-4R7M-1, rated at 1.1A (ITemp) and 1.2A (Isat).
I was able to pack the components onto a 14mm x 8mm PCB, which I ordered in 2oz. copper from OSH Park. When the board arrived I found out that I did not have a 22uF 0805 cap with a voltage rating above 16V, so I used a 1210 cap instead.
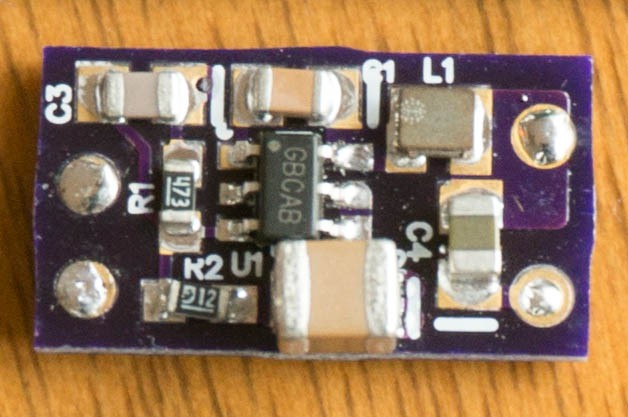
It fit...just barely. Weighed in at 0.48g. Not bad.
I tested just a few parameters so far. Output voltage = 4.97V, over a 7V - 25V input range. It will put out 650mA continuously (with no measurable voltage drop), but gets too hot and shuts down with a 1.3A load.
The output ripple voltage is about 20mVp-p (no load), and pretty clean.
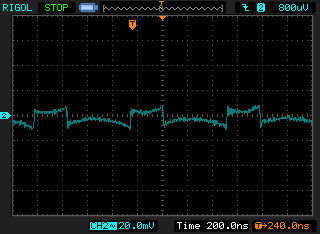
I took some efficiency measurements at a few load currents:
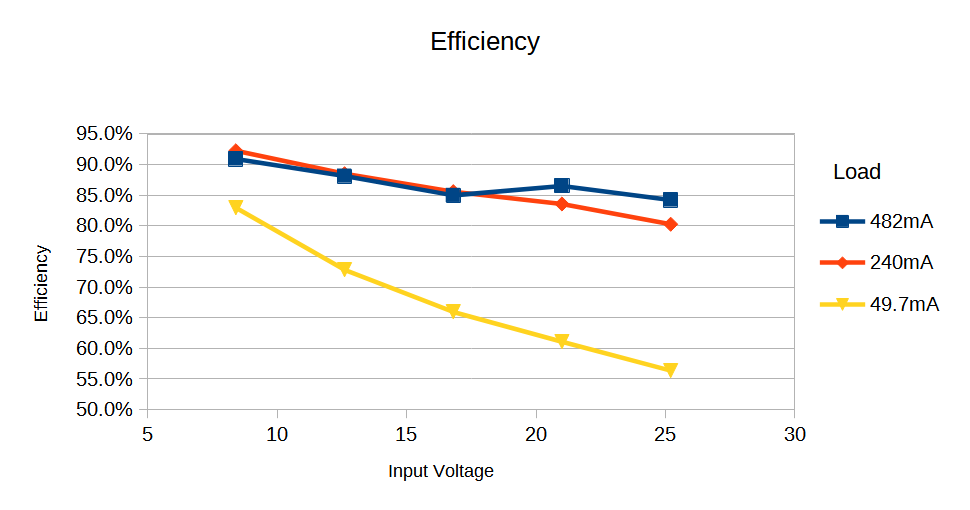
Sidebar: Switched-mode converter vs. Linear Regulator Efficiency
You might look at the chart above and think "Why is he doing this for a lousy 56% efficiency? I'm just gonna use a linear regulator." Well let's examine that thought.
For the "poor" efficiency case above the converter was outputting 250mW, and was requiring 450mW input power. That's a loss of 200mW. An ideal linear regulator would consume 1.26W, with a loss of 1.01W. That still doesn't seem so bad until you consider the temperature rise that 1W of power would produce on these tiny PCBs.
My fat finger estimates that the thermal resistance of a 10mm x 10mm PCB in free air would be around 100C/W (maybe more). Here's a plot of thermal resistance vs. PCB area from the MIC2876 datasheet. To add insult to injury, the converter will probably be covered with heat shrink tubing.
The buck converter temperature rise would be around 20C, where the linear regulator would cook at 100C. I can leave my finger on the buck regulator without getting burned (<50C), but I'd get a blister from the linear regulator after a couple of seconds. And that is just for a 50mA load current.
Things get worse with higher load currents. At Vin = 25.2V, with a 500mA load current, the buck converter efficiency is about 85%. That's...
Read more »
Cool project. Have you been able to take any efficiency measurements?
Also--how are you planning to solder the UDFN package? For my projects, I use the toaster oven reflow method, but I've found that leadless packages have a low success rate.