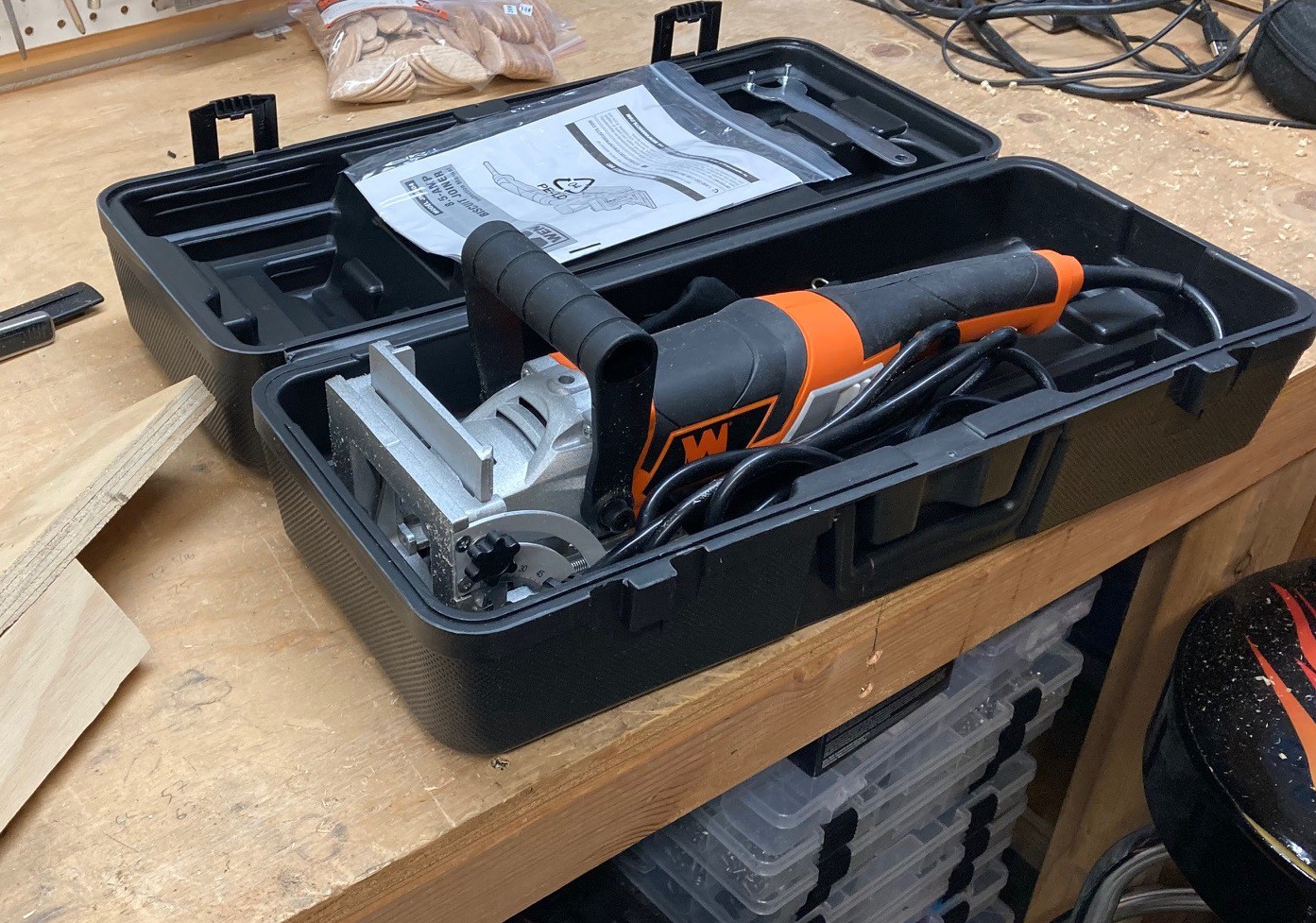
My biscuit joiner came in! It was crazy cheep at around $50. I picked this one over the harbor freight or grizzly model mostly because it came with a nice blown plastic case.
I spent some time with the calipers and a square verifying it was all put together well, it seems well built for the price. There is a bit of slop side to side on the main axis of motion but the more important vertical play is very minimal. The fence has a tiny bit of slop in it but for the most part it works well. I had a look at a porter cable model at woodcraft and it was very close in feel to this one with similar amounts of play.
One negative is that the springs on the plunge are a bit stiff. It really takes 2 hands to push this into the material. That is fine because this also does not have a soft start feature and it really jerks in your hands if you try to start it up one handed. You really need to clamp everything down well before using this (or any plunging spinning blade of death).
I did a quick test on some very warped and un-square scraps and it worked out surprisingly well. I measured only 0.2 mm of tilt in the slot across the full plunge depth. And the included biscuits fit nice and tight in the slot and held everything together very well. I'm looking forward to trying this out on something more serious.
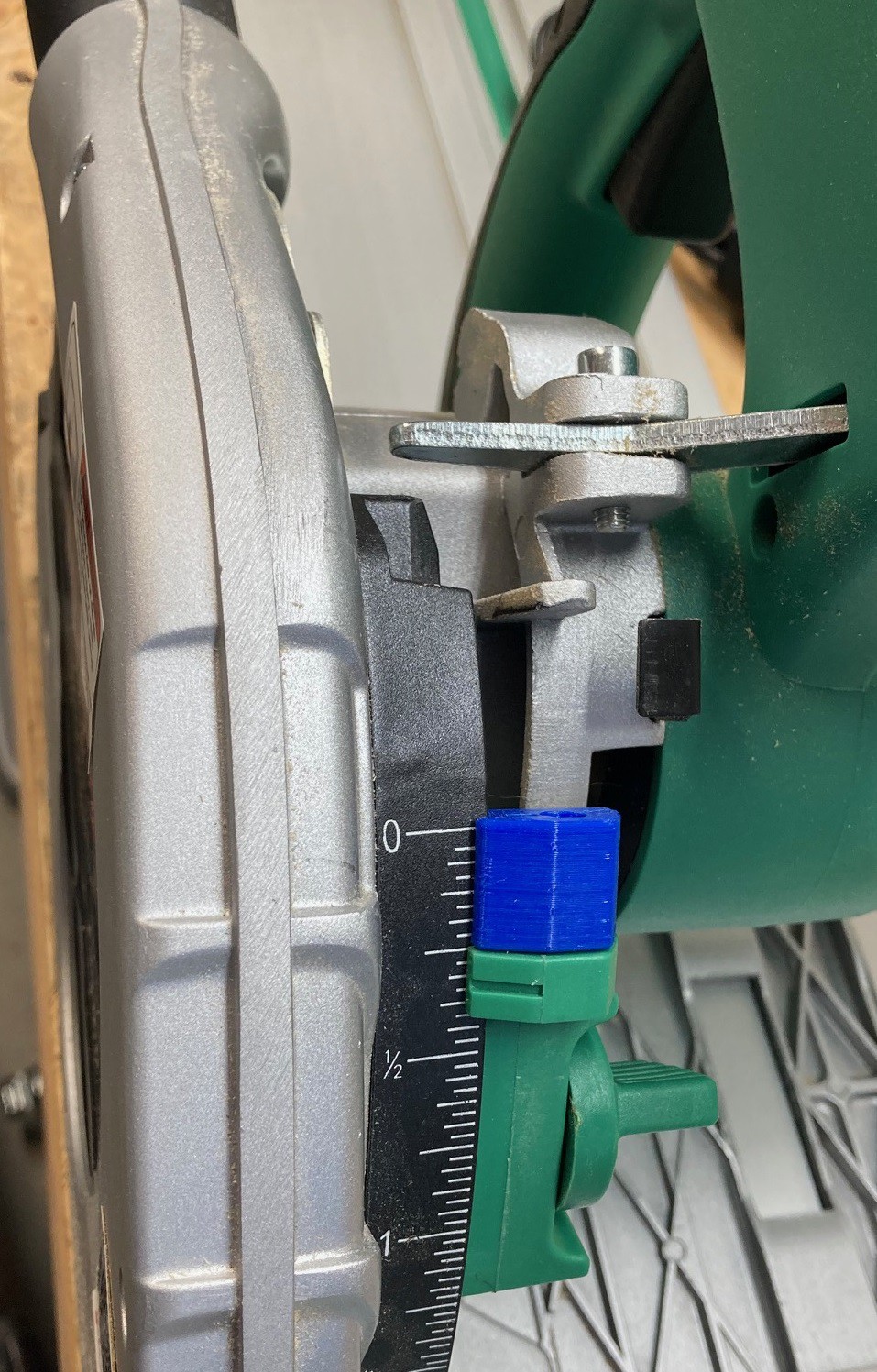
My track saw has a very annoying flaw. The indicator on the depth gauge is off by 5/8". It took me too long to figure this out, I kept setting my blade with plenty of room and it kept coming up short. I went through lots and lots of ideas on how to fix this, but eventually just printed a small spacer out to move the edge of the indicator up 5/8" of an inch. I attached this with a dab of CA glue, I think it will hold up well enough. I could just remember it is off, but that is bound to bite me eventually. Honestly I have been over this several times and can't see how they messed it up. Maybe it was originally designed for a larger blade.
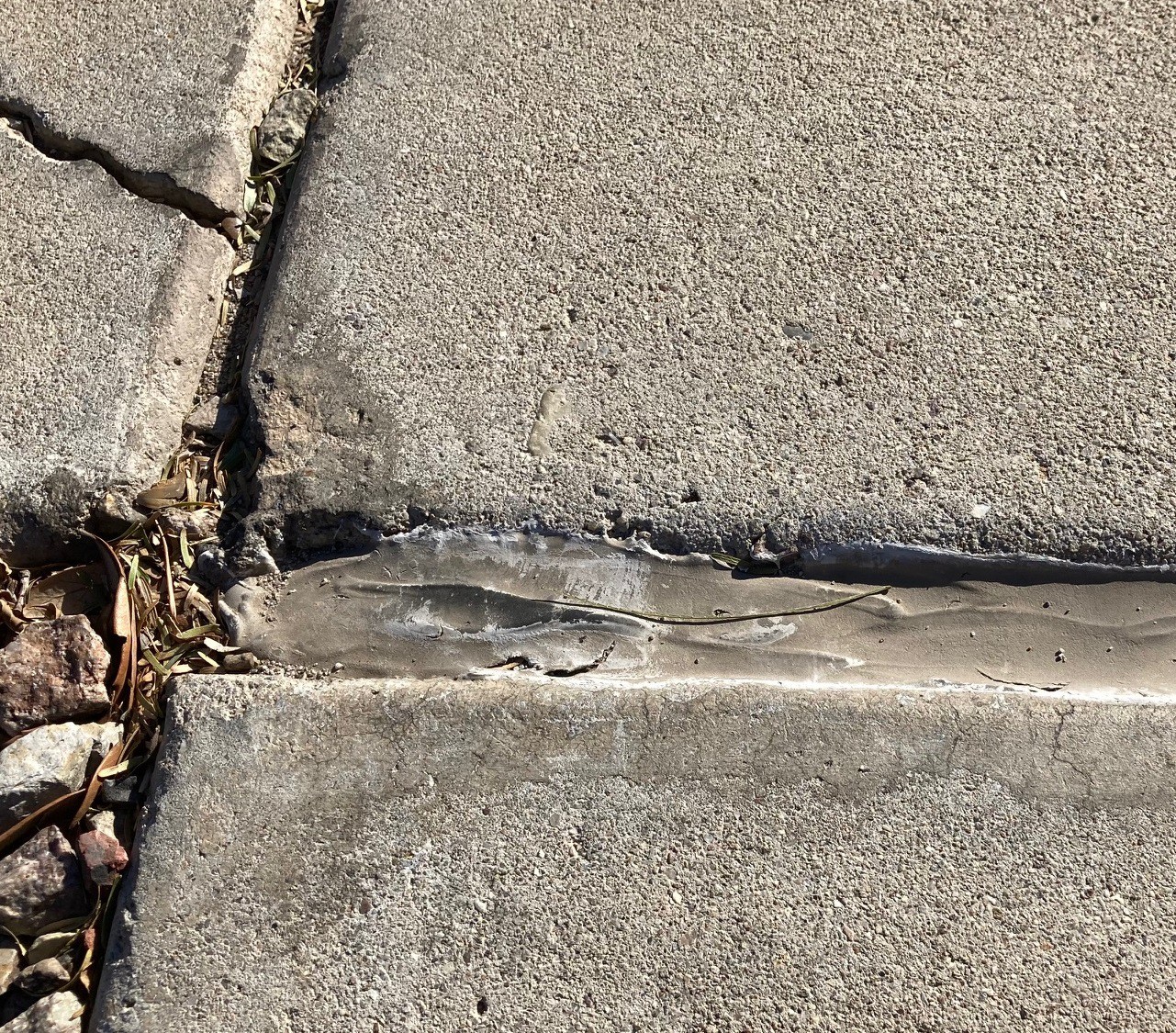
I was out for a walk and noticed that my neighbor had filled in there expansion joints with foam sausage and some silicon. This was an interesting chance to see how this hold up and how it looks. It does not look that good and has not held up that well either and the foam sausage is not very stiff so it is fairly squishy as well. However it was not completely terrible, and I would be applying this indoors so it should hold up better.
One idea I have been thinking about is filling the crack with sand, then using a 1/4" layer of calk to seal it in. That may work better and provide more support than the sausage, without needing several cubic feet of sealer. I'm not sure if sand is a good idea, it won't compress that well, but should handle expansion just fine.
I'm a little behind the times, I just discovered the Festool MFT table. I was able to see one in person at woodcraft. It feels a bit rickety but I really like the idea of the elevated track that is held at a right angle to the workbench and using bench dogs to align and hold down the material.
I can't afford a festool keychain let alone a workbench, but this does not look that complicated to make yourself. I have a small CNC that could cut out a template, then using a router I could copy the holes into a sheet of MDF. It would cost very little to put together. However I would end up with lots of holes in the worktop, so I would need to make some sort of a torsion box so I can fit clamps into it and so material can fall through the holes.
The bigger concern I have is how much would it cost to get the bench dogs and clamps and other accessories. There seem to be several lower cost copies from China but even these are quite expensive. I have a 3D printer, so I could 3D print most everything as a first pass, however I'm not sure how well those would hold up over the long hall.
Another issue is that my workbench is going to be rather small, so this would only be useful for smaller cuts. At best I could handle a 30" width of material, not exactly amazing. Still this is a more modern take on a workbench, so it is worth thinking about.
I will soon have a lot of material to break down and so I was looking around for some ideas on how to make this go smoother. There are these fancy parallel guides you can get for festool style tracks for $100 or so, but my tracks don't have the right slot to use these, and there a bit expensive.
Another idea would be to get a square for the end of my track. They range from $30 to $60, but I think I can make one on my CNC out of MDF fairly easy for free.
You can get these extensions for the square that allow you to repeatable make a cut from the edge of the board. This is basically a poor mans parallel guide system. Together this is runs about $110, or basically the same as the parallel guide system, but it offers two different ways to reference the edge of the board.
Again I can't really afford all of this, but I could build something similar out of wood or 3D print it. It is something to experiment with.
Discussions
Become a Hackaday.io Member
Create an account to leave a comment. Already have an account? Log In.