A slew of power outages motivated the lion kingdom to think more seriously about a flashlight instead of a phone or a $1 thing from 10 years ago. The last proper flashlight in this apartment came 20 years ago. There's a lot of nostalgia these days for vintage lanterns with big old lantern batteries.
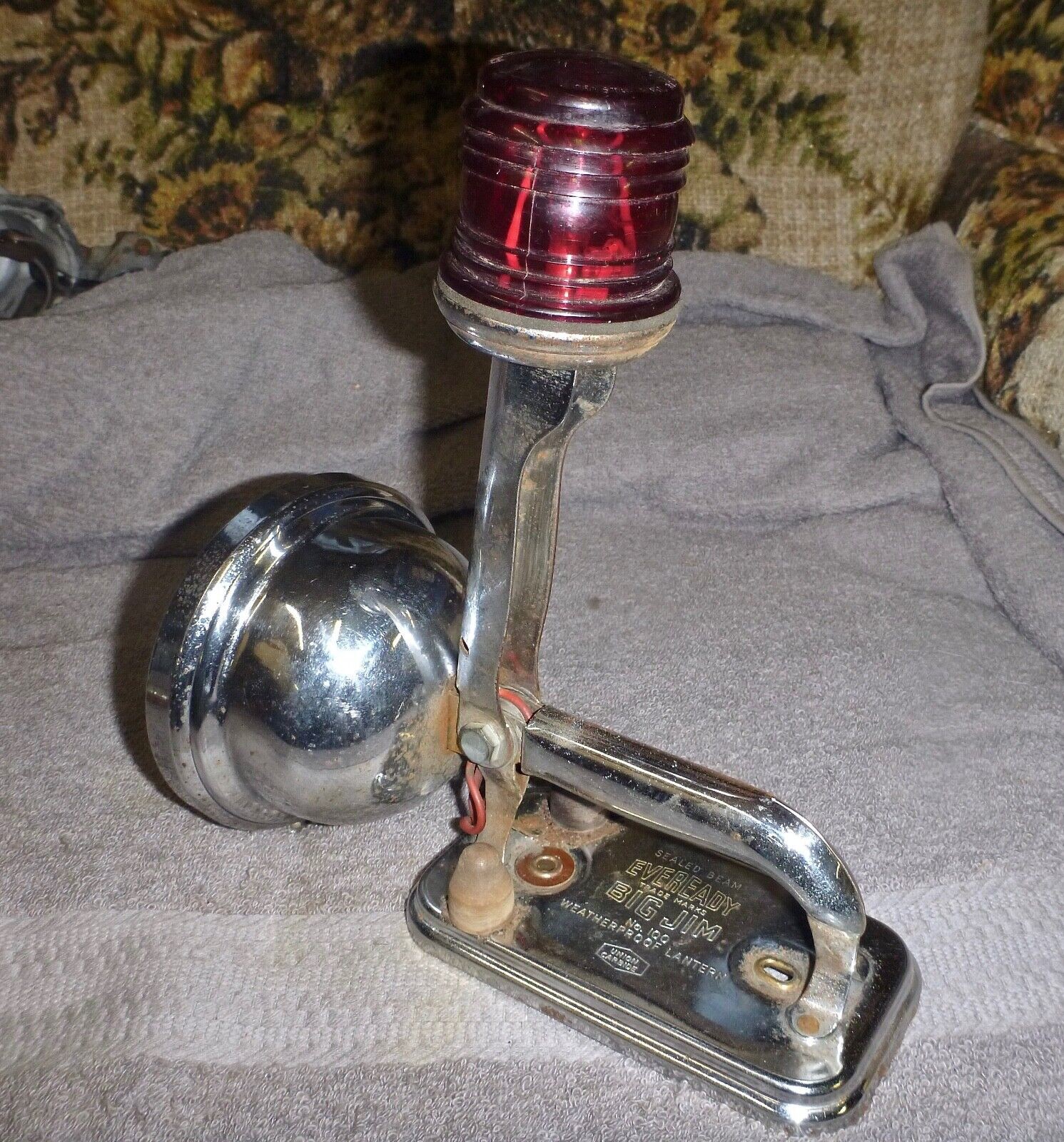
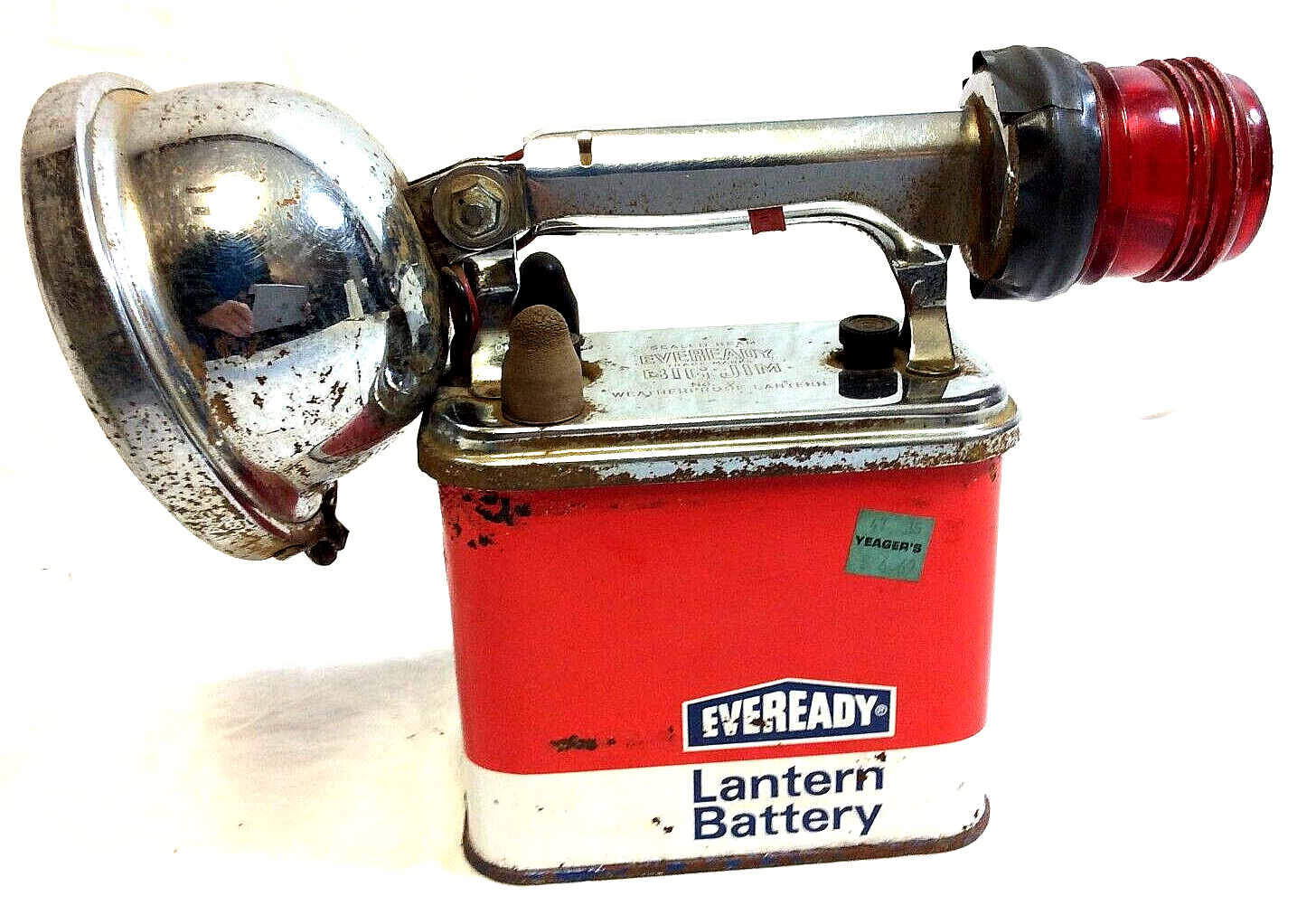
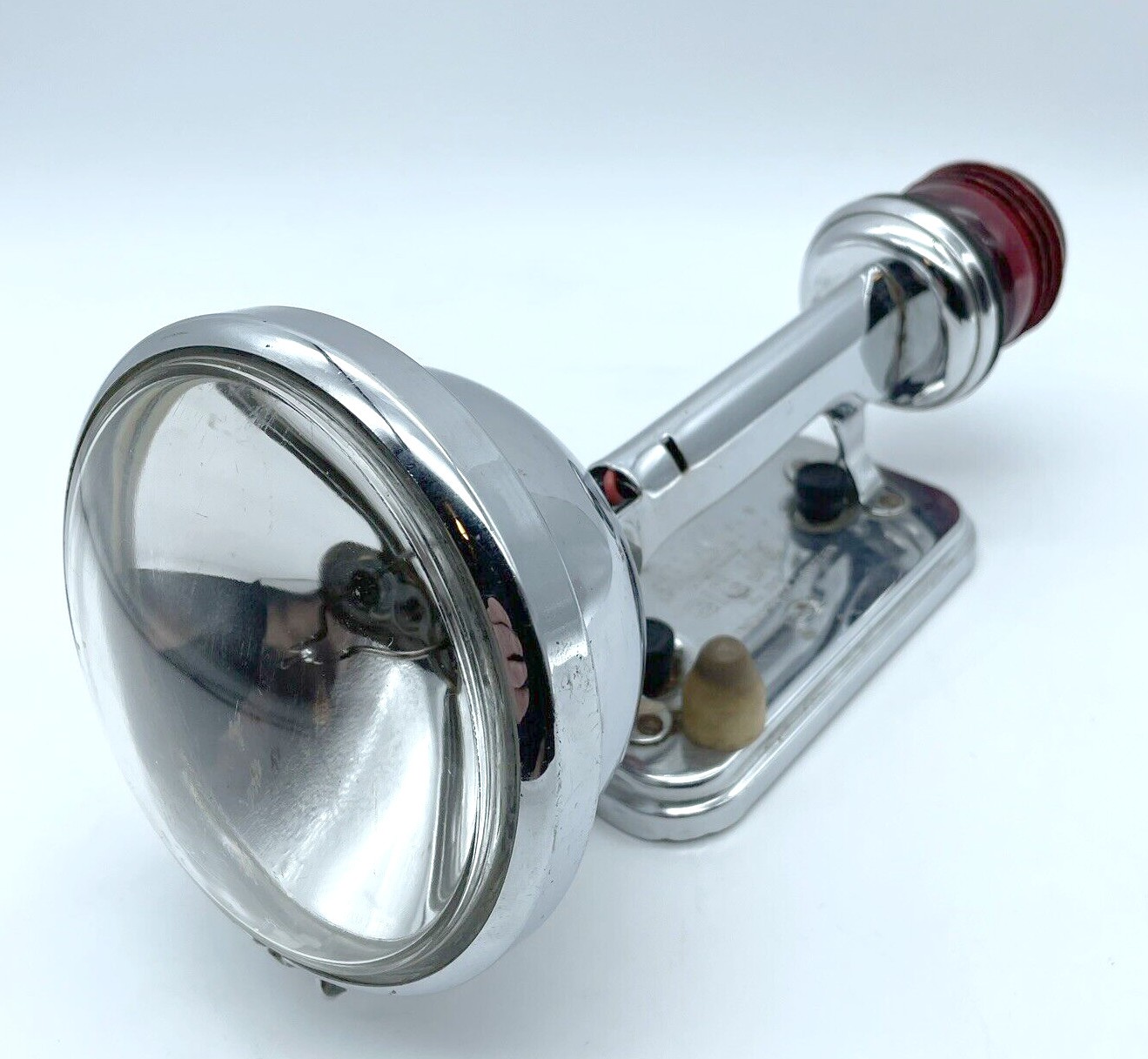
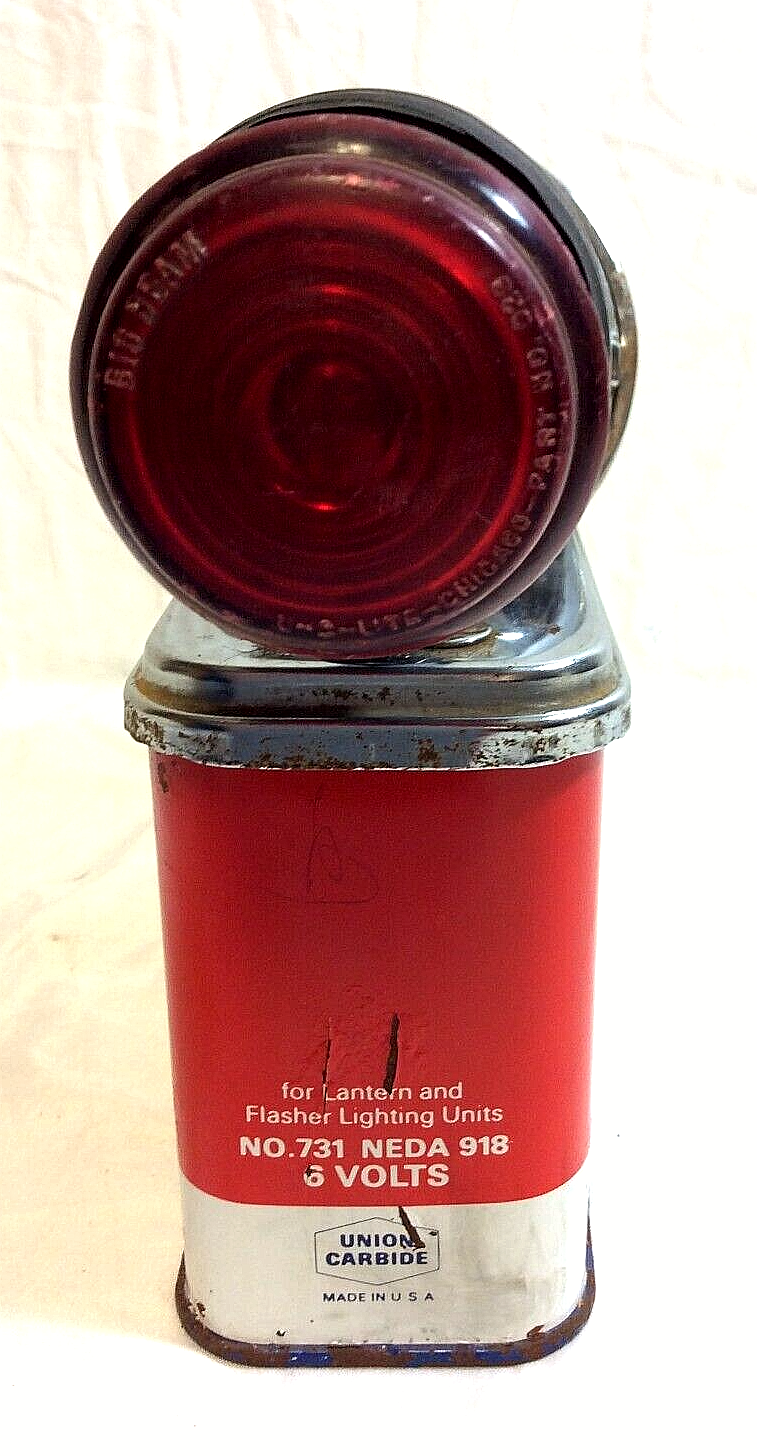
The $6.69 zinc carbon battery pictured is now $5.50, which gives an idea of why housing inflation has to be so high in an inflation targeting system.
The full vintage experience is a bit too large but it does need a pivoting lightbulb. There would be 2 lights with the same pivoting lightbulb idea. 1 is a replacement for a manes voltage light, based on the big jim 100. It straps on to a big 12V lipo. It doesn't have the red light. It has a 9W LED lightbulb. It needs a battery level, SEPIC converter, & brownout protection. A heat sink has to bolt on to the light bulb.
1 is a pocket flashlight replacement. It needs long term standby batteries, so 6V nimh regulated down to 3.3. It has a spot beam.
The lightbulbs go from straight up to straight down with a friction mechanism. They both need to stand vertically. A folding thing comes to mind, akin to the folding nose cone already made.